Цементация железа является крайне важной технологией, в которой попаданцу стоит хоть немного разбираться.
Процесс науглероживания железа при контакте с раскаленным углем был открыт очень давно, и, вероятно, был одной из движущих сил быстрого перехода из бронзового в железный век. Раньше всего было замечено, что выплавка железа в сыродутном горне при определенных условиях может приводить к крицам из сырцовой стали, которую с глубокой древности отличали от простого железа. Поверхностная цементация орудий из мягкого железа также известна по крайней мере с VIII в до н.э., а вероятно, и сильно раньше, но установить это сложно из-за сильной коррозии железных артефактов. Такое науглероживание проводилось или в горне в толстом слое углей, обеспечивающих восстановительную атмосферу, или путем нанесения слоя органических веществ, покрываемого для защиты от выгорания глиняным чехлом. Например, для цементации напильников смазывали насеченную заготовку салом, обматывали ремешками из кожи и льняными нитками, обмазывали глиной и нагревали, и после длительной выдержки закаливали в воде. На Руси цементация широко использовалась для производства уклада – ковригу из кричного железа многократно науглероживали в горне с углем и резко охлаждали ледяной водой или снегом. Закалившуюся поверхность отбивали молотом и сталистые пластинки собирали в пакет, который затем проваривали и проковывали, получая весьма однородную сталь.
Долгое время считалось, что превращение железа в сталь состоит с очищении железа от ненужных примесей при длительном контакте с огнем. Лишь в середине XVIII в Реомюр, активно исследовавший процесс цементации, понял, что ситуация ровно обратная – железо поглощает «летучие сернистые соединения» (так в то время называли все горючие составляющие материи) и превращается в сталь, а еще позже – в 1786 г. – Вандермонд, Бертолле и Монж опубликовали статью, в которой описали железо, сталь и чугун как сплавы с разным содержанием углерода.
Следует различать цементацию готовых изделий с целью повышения поверхностной твердости и получение цементной стали. Цементация поверхности в твердом карбюризаторе – это достаточно простой процесс. Достаточно поместить железные предметы в угольный порошок (лучше всего из березового угля, еще лучше – животный уголь из отходов кожи , рогов и копыт; в настоящее время используют древесный уголь с добавлением активаторов – карбонатов натрия, калия или кальция) в соответствующей огнеупорной емкости, защищающей уголь от выгорания, а метал от окисления, и нагревать достаточно продолжительное время. Если нужно цементировать не всю поверхность, то следует покрыть ненужные участки глиной, медью или полудой. Хотя процесс и называется цементацией в твердом карбюризаторе, в действительности поглощение углерода идет из газовой фазы – при высокой температуре монооксид углерода разлагается на углекислый газ и элементарный углерод, который поглощается поверхностью железа. Образовавшийся углекислый газ реагирует с углеродом карбюризатора с регенерацией окиси углерода. Стандартный режим цементации – 900-950 °С (легко достижимо хоть в дровяной печи), при этом за 1 час толщина науглероженного слоя увеличивается примерно на 0.1 мм. Обычно сразу после такой обработки предметы подвергаются закалке, которая и сообщает высокую твердость наружному осталеванному слою. Скорость науглероживания при повышении температуры сильно возрастает, и науглероженный слой в 1 мм можно получить уже за 4-5 ч при 980-1000 °С, но, поскольку перегретая высокоуглеродистая сталь дает хрупкую крупнозернистую структуру, потребуется еще несколько раз проводить нормализацию перед закалкой. Поверхностная цементация улучшает только поверхность металла – меч, например, изготовленный из очень низкоуглеродистого железа и покрытый стальной коркой в 0.5 мм, погнется при первом же ударе. А вот для ножей, серпов, столярного и слесарного инструмента, наконечников стрел и дротиков – это отличный вариант. Цементация необходима для всех деталей ударно-кремневого замка (кроме пружины), цементированными были до начала XX в. многие другие части огнестрельного оружия (рамки и барабаны револьверов, ствольные коробки, колодки ружей-переломок – все эти детали ковали из того же мягкого железа). В XIX в получила распространения цветная калка, при которой цементацию тщательно отполированных и обезжиренных деталей проводили в смеси древесного и костяного угля, а потом сразу закаливали детали в воде, получая твердое покрытие радужных цветов.

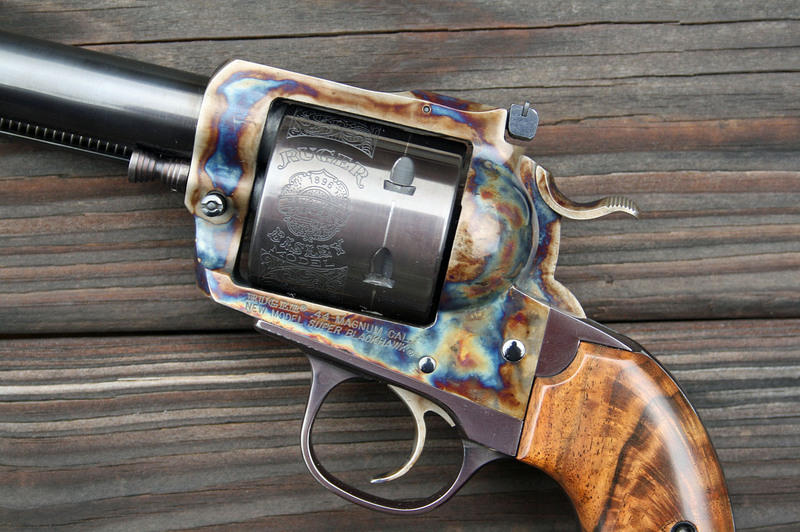
С появление броненосцев цементация в сочетании с поверхностной закалкой широко применялась при производстве броневых листов – только так можно было получить броневые листы с очень твердой лицевой поверхностью и вязкой основой. Для броневых плит стали применять газовую цементацию, с использованием светильного газа или ацетилена, а потом и просто керосина как источника углерода.
Очевидно, если продолжать цементацию достаточно долго, то науглероживание железа произойдет во всем объеме. Такой процесс в промышленных масштабах стали использовать в XVI-XVII вв в Германии и Англии, и, с разными модификациями, применяли вплоть до 1950-х годов. Полосы железа помещались в корыта из огнеупорной глины, вделанные в специальную цементовальную печь.

Полосы укладывались как можно плотнее, но с обязательными промежутками около 20-30 мм, плотно заполненными угольным порошком, при этом за одну загрузку цементировали от 2 до 25 тонн железа. Для защиты от окисления сверху насыпали толстый слой мелкого песка, и растапливали печь, постепенно повышая температуру. Из-за низкой теплопроводности угольного порошка только на прогрев уходило до нескольких дней, после чего температуру повышали до максимальной. При высокой температуре цементация происходит достаточно быстро, но тем не менее для больших загрузок железа печь приходилось топить 1-2 недели, при этом самое главное было не перегреть печь, потому что можно было получить оплавление поверхности полос или переуглероживание с образованием чугуна. Поскольку цементация была достаточно затратным процессом, сталь делали только из лучшего и самого чистого от примесей серы и фосфора железа – в Англии использовали только шведское древесно-угольное железо из определенных мест производства. После охлаждения печи полосы стали (в Англии ее называли blister steel из-за характерных пузырьков на поверхности, а в России – морянкой или томленкой) сортировали, и для изготовления нужных вещей проваривали под молотом, или переплавляли в тигле. Аносов, обнаруживший газовую цементацию, использовал этот процесс очень оригинально получения литой стали – куски железа в открытых тиглях при достижения нужного содержания углерода плавились и стекали на дно тигля, при этом слой флюса защищал металл дальнейшего превращения в чугун.
Кроме цементации для попаданца может быть очень интересен процесс цианирования, про котором железные детали помещают в ванну с расплавленными цианидами (обычно смесь соды или поташа с цианидом натрия или калия, можно использовать и желтую кровяную соль K4[Fe(CN)6], которая при нагреве разлагается с образованием цианида калия). Цианирование приводит к насыщению поверхности углеродом и, в небольшой степени, азотом, при этом процесс в жидкой ванне идет гораздо быстрее (при 850 °С слой в 0.5 мм можно получить за 1-2 часа), поверхность получается еще тверже (за 70 HRC), и практически не происходит коробления деталей, что часто случается при цементации тонкостенных изделий.
Процесс обратной цементации, а именно удаление избыточного углерода из чугунных изделий, может быть не менее полезен. Обратная цементация была обнаружена Реомюром в ходе его многочисленных экспериментов, хотя в Китае подобный процесс использовался задолго до этого. В XIX в получаемый металл под названием ковкого чугуна (это не совсем то, что сейчас подразумевается под ковким чугуном) широко использовался для массового изготовления небольших изделий, в том числе деталей замков оружия и даже, например, рамок револьверов и колодок двухстволок. Исходный чугун должен быть белым, с минимальным количеством кремния, серы и марганца, лучше всего такой чугун получать цементацией и переплавкой железа с древесным углем. Отлитые детали помещались в тигли с веществами, способными отнимать углерод – железной рудой или окалиной, и нагревались в печах при температуре около 950-1000 °С в течении 60-80 ч, при этом углерод диффундирует к поверхностным слоям и окисляется кислородом, так что его содержание падает примерно до 1%. Кроме выгорания, часть углерода из цементита переходила в мелкодисперсный графит, как и в современном ковком чугуне. В зависимости от условий охлаждения, можно получать металл с распределенным графитом и разной микроструктурой сталистой матрицы.
а некоторые все периодически рассказывают о «золотых» напильниках https://youtu.be/WJdWzm8crsQ?t=304
Это может показаться удивительным, но ранние револьверы Кольта — и Патерсон, и легендарный Уокер — производились практически полностью из сварочного железа. Сталь, скорей всего импортная английская, была только в пружине. Ствол, по-видимому, изготавливался ковкой. При производстве Уокера с большим трудом подобрали подходящий материал для барабана, выдерживающего выстрел пулей .44 калибра с 3.6 г пороха. Для револьверов меньщих калибров требования к металлу были существенно ниже.
Рамки не только из железа, но и из бронзы и даже ковкого чугуна. Стальные стволы и барабаны стали делать только в 1850-х, а на заводах Кольта — с 1860-х (под рекламным названием «серебрянная пружинная сталь»).
А откуда инфа?
Меня в первую очередь стволы интересуют. А то как то раз меня уверяли что нарезняк в 19 стал распространен только благодаря пудлинговой стали.
https://books.google.ru/books?id=K6t0DQAAQBAJ&pg=PA13&lpg=PA13&dq=colt+walker+wrought+iron+cylinder&source=bl&ots=52UDAgUhES&sig=ACfU3U3uJF1POSECKYQ-C8ISk_Vu39bLRA&hl=ru&sa=X&ved=2ahUKEwio_fa—qfsAhUNiYsKHej9A1o4FBDoATAHegQIABAB#v=onepage&q=colt%20walker%20wrought%20iron%20cylinder&f=true
https://www.lodgewood.com/Colt-Prototype-Army-Revolver-Copied-from-William-B-Edwards-THE-STORY-OF-COLTS-REVOLVER_c_280.html
https://thefiringline.com/forums/showthread.php?t=424112
А вот здесь интересная статейка по оружейной металлургии в 1850-х в сша http://www.jstor.org/stable/40968024
Вообще Кольт активно экспериментировал с металлом, и драгунский револьвер 1848 уже получил барабан из стали.
Пудлинговое железо не имело никаких преимушеств (а скорей недостатки) кроме больших объемов производства и возможности пудлинговать любой чугун. И нигде, кроме Англии, его по сути и не использовали — в основном использовалось (для нарезного тоже) крично-передельное железо. Вполне годилось и сыродутное.
Ключевым фактором, заставившим всех оружейников искать лучший металл, стало внедрение заварки стволов на вальцах, для чего требовалось очень хорошо проваренное железо (при ручной заварке трубку очень хорошо проковывали, выжимая заодно дефекты). А затем полное перевооружение на нарезное оружие — железные стволы имели низкий ресурс, приемлемый для охотничьего или егерьского оружия, но абсолютно непригодные для массового вооружения. Практически везде эту проблему рещили переходом на тигельную сталь.
Вот здесь про Россию в XIX в
http://www.artillery-museum.ru/assets/files/konferenciya_vio_2016_v_tom_cv.pdf стр.386
// А затем полное перевооружение на нарезное оружие — железные стволы имели низкий ресурс, приемлемый для охотничьего или егерьского оружия, но абсолютно непригодные для массового вооружения. Практически везде эту проблему рещили переходом на тигельную сталь.
В первую очередь меня интересуют нарезные мушкеты, а их часто переделывали из обычных.
Насчет «полностью непригоден» не уверен — в том же последнем источнике пишут что тигельная сталь позволяла делать стволы «практически вечными», те тут скорее речь о избыточной надежности. Полезно, но не обязательно.
Про те же витые гильзы часто пишут что дескать они были оч плоххими. Но на первых испытаниях они дали отличный результат. В плохом действии в Африке была виновата армия, не испытавшая смазку в жарком климате и переснаряжавшая гильзы по десять раз. Но чтобы принять тянутые гильзы витым устроили плохой пиар.
Возможно и с кованной сталью для нарезняка то же самое, и конкретные цифры приемлемы.
Переделка ружей в нарезные, а потом и казнозарядные везде была вынужденной, временной мерой. Тяжелая цилиндро-коническая пуля в 6-7 линий требовала уменьшения порохового заряда и приводила к отвратительной баллистике. Расстрел (и износ от чистки) ружей первой половины XIX в доходил до половины линии, в нарезном варианте — гораздо быстрее. Дело не в прочности стенки ствола — ружья и мушкеты имели солидный запас прочноси (например, ствол, рассчитанный на заряд в 8.6 г пороха, выдерживал проверочный выстрел зарядом в 43 г пороха с двумя пулями), а в абразивном износе и разгаре.
// Расстрел (и износ от чистки) ружей первой половины XIX в доходил до половины линии
А на сколько выстрелов? Поллинии это порядка мм, стандартный зазор и так был 1.5-2 мм.
// the Prussian Nothardt muske had reduced windage of 0.04 inch, but this caused extencive fouling and much greater recoil.
// Foard (2009), mentions in his research that the average amount of windage was 1.5 mm.
«Подробное наставление о изготовлении, употреблении и сбережении огнестрельного и белого солдатского оружия», Гогель
глава Срок службы огнестрельного оружия
описывается два французских эксперимента с расстрелом 4 градкоствольных ружей по 25000, и 4 по 10000 — никакого износа ствола. Разболтались детали, одно ружье разорвало, скорее всего от неправильного заряжания.
еще российские опыты 1822 — 2000 выстрелов из 6 ружей — затравочные отверстия увеличились, ствол расширился на одну восьмую линию в глубине ствола, те на точность влияет слабо.
—
Для нарезняка таких хороших данных не находил. (
Попадались
http://americanlongrifles.org пара сотен выстрелов до обновления это оценка снизу.
>> I’ve put at least 100 patched balls through it with no wear that I can detect. Shoots as close as I can hold it, with a .350 ball and .018 patch.
>> Suppose that a barrel ONLY lasted 200 shots before the bore needed freshing out. I doubt many colonials fired their rifles more than a couple of times a month to harvest a deer or hog (unless they got into a pitched battle with raiding Indians at which time the issue of barrel maintenance probably transferred over to the Iroquois or Cherokees). At that rate, every 100 months/8 years the gun would go in for freshing.
freshing — были специальные резцы, была у меня картинка в закромах, но найти не могу, обновляли края нарезов
но сколько обновлений выдерживал ствол нигде на находил (
На переделку только ружья в хорошем состоянии или вообще со складского хранения, и их развертывали на одинаковый калибр перед нарезкой — для гладкоствольного зазоры 1.5 мм сойдут, для нарезного, даже с расширяющимися пулями — нет.
В процессе эксплуатации нарезных ружей износ не толтько от стрельбы, но и от коррозии и растирчния дульной части шомполом. Даже покрытым медью шомполом можно убить дульный срез очень быстро, после чего прийдется укорачивать ствол.
Ресурс перед фришеванием — хз, но наверное до 500 при аккуратном обращении.
Само фришевание производилось свинцовой пробкой, отлитой в канал ствола. Туда вставлчлись резцы и прогонялись с подкладыванием бумажек, как и при нарезании.
https://piterhunt.ru/library/books/voprosy_oruzheinoi_tekhniki/frishevanie_chistka_narezov.htm
http://www.flintriflesmith.com/ToolsandTechniques/freshening.htm
Если срезать по 0.1-0.2 мм, то нарезов шириной 3-4 мм хватит на 5-10 процедур.
Имхо тут вопрос в скорости экономического роста.
Тот же Гогель упоминает срок службы ружья в 40-50 лет. Тогда ресурс в несколько тысяч выстрелов нарезняка с гемморной чисткой нарезов выглядит критическим недостатком.
Но при потенциальном быстром попаданческом росте, когда понятно что через десять лет будет уже другое технологическое поколение, нарезняк из кованного вполне себе интересен.
Мне кажется, что проблема износа не так уж критична. В случае поражения в битве теряются значительная часть ружей, при поражении в войне теряется вообще всё. Кормление, одевание, обучение солдата обходится очень дорого. Стоимость даже очень дорогих ружей на фоне всего этого кажется уже не такой большой. И если солдаты будут стрелять даже на 20% дальше, чем противник, это окупит двухкратно большую стоимость и двукратно меньший ресурс после первой же битвы.
Очень сомнительно. Одежда и пища добровольно-принудительно (налоги и прямой грабёж) реквестируются у населения, обучением занимаются точно такие же «старослужащие», а огнестрел требует очень нехилой металлургии и «заводских» мощностей с крайне дефицитными техническими специалистами. Что выливается в огромную стоимость хоть сколько то вменямого огнестрельного оружия и более чем актуальность методов уменьшения износа. ПРи этом солдат всегда можно набрать новых и одно ружъё на троих пусть и хуже трёх ружей на троих, но куда лучше втрое меньшего количества солдат.
// выливается в огромную стоимость хоть сколько то вменямого огнестрельного оружия и более чем актуальность методов уменьшения износа
А теперь цифры.
Стоимость ружья в 18 веке на Руси — 1-2 рубля. В военное время срочные закупки могли идти и по 10-20 рублей, но это именно доплата за срочность, а не себестоимость.
// Антуфьев снизил до 1,8 рублей за штуку.
// большинство казачьих офицеров от квартирмейстеров до есаулов получали всего по 9 рублей.
// 1768 год … средние расходы казны на армию 29 рублей на военнослужащего
// К самым низкооплачиваемым … месячный оклад барабанщика штаба Полицейской канцелярии составлял 38 коп = 5 рублей в год
Есть ньюанс: цена для полноценно воюющей армии, когда велик риск потерь, идёт мобилизация и т.д.
И цена для армии мирного времени, либо армии воюющей исключительно выигрышные битвы (курощение мелких соседей, «принуждение к миру», «полицейские акции» и прочее…).
И это две принципиально разные цены и идеологии в оружии.
// Что выливается в огромную стоимость хоть сколько то вменямого огнестрельного оружия
Не совсем верно. Сложность одного образца конечно поднимает цену но проблема МАССОВОГО производства несколько в ином.
ситуация одна винтовка на троих бывает из-за малого числа заводов, а не из за сложности одного образца. Мосинка была простой, но царская Россия не смогла обеспечить нужный объем производства, да и не осознавала объемы необходимые для ПМВ (впрочем этого никто не осознавал, проблемы с оружием были у всех сторон).
Как верно указал Ваш1, цена ружья составляет примерно месячное жалование солдата. (Годовое жалованье солдата при Александре I составляло около 10 рублей. Кроме этого, полагалось в год 72 «мясные» и 15 «соляных» копеек.) Офицеры суммарно получают денег больше чем солдаты которыми они командуют. т.е. если солдат будет менять ружье даже раз в год это поднимет денежные затраты на один -два процента. Не настолько страшная сумма, не так ли?
Вот только заводы могут не справится с такой нагрузкой, их придется построить побольше и откуда-то взять квалифицированных рабочих… А эта задачка просто за деньги не решается.
«при высокой температуре монооксид углерода разлагается на углекислый газ и элементарный углерод, который поглощается поверхностью железа»
Копать не копал, но предположу, что поглощается металлом именно СО, в какие-то нестехиометрические ферроценообразные комплексы, и уже они в металле разлагаются. Иначе газовая фаза, IMHO, не так критична была бы.
Это, кстати, и с цианированеим процесс роднит.
При 1000 градусов контранта равновесия между карбонильными (при чем тут ферроцен?) комплексами и железом пренебрежимо мала.
А разложение СО на поверхности ясен пень идет через хемоадсорбцию.
> при чем тут ферроцен?
Пардоньте, у меня визуально карбонильно-циклопентадиеновый комплекс вспомнился, как производное ферроцена… Чистая карбонильщина конечно.
> При 1000 градусов контранта равновесия между карбонильными комплексами и железом пренебрежимо мала.
А вот я не знаю, как её оценить — для сорбции СО где-то по границам зёрен. И где граница между хемосорбцией и образованием чего-то многоядерного нестехиометрического… с одной стороны вросшего в металл, с другой — частично комплексованного.
При большом желании и гвоздь с адсорбированеым на поверхности монооксидом углерода можно назвать нестехиометрическим карбонильным кластером, но зачем?
Дык за механизмом. Мне исходная фраза «монооксид углерода разлагается на углекислый газ и элементарный углерод, который поглощается поверхностью железа»» не понравилась. СО поглощается, возможно даже куда-то диффундирует (а-ля лиганд, по дефектам), а уже потом разлагается, не наоборот.
Это к тому, почему просто натереть углём и погреть — малоэффективно. Хотя поверхностная концентрация С с углём может и выше быть.
«Цементация стали осуществляется атомарным углеродом. При
цементации твердым карбюризатором атомарный углерод образуется
следующим образом. В цементационном ящике имеется воздух,
кислород которого при высокой температуре взаимодействует с углеродом карбюризатора, образуя окись углерода. Окись углерода
в присутствии железа диссоциирует по уравнению 2СО -> С02 +
+ сат.
Углерод, выделяющийся в результате этой реакции в момент
его образования, является атомарным и диффундирует в аустенит.
Добавление углекислых солей активизирует карбюризатор, обогащая
атмосферу в цементационном ящике окисью углерода: ВаС03 +
+ С ВаО + 2СО.»
Ю. М. Л а х т и н. Металловедение и термическая обработка металлов. Учебник
для вузов. 3-е изд. М., «Металлургия» страница 234
Для попаданца может быть полезен способ химико-термической обработки, известный как тенифер-процесс, или низкотемпературное азотирование в солевых ваннах. Азотирование происходит при 500-600 гр в расплавах цианидов или цианатов в смеси с карбонатами. В современном варианте цианистые соединения получаются прямо в ванне при добавлении в нее дициандиамида, меламина и подобных соединений. Попаданец же может использовать свой любимый реагент — мочевину, которая при сплавлении с карбонатами как раз и дает цианат. Азотировпнние в расплаве происходит достаточно быстро, в течение нескольких часов, и дает коррозионно- и износостойкую поверхность, а при использовании легированных сталей — очень твердую (нужно как минимум 1% хрома, титана, алюминия, волфрама или молибдена). Тенифер-процесс применяется, в частности, некоторыми производителями оружия.
Если попаданец захочет реализовать такую обработку стволов для увеличения их ресурса, то кроме проблемы дефицита мочевины нужно будет как-то получить легированную сталь. Сыродутным способом такое железо не сделать, а вот кричным переделом — может и получится. Хром сильно усложняет кузнечную сварку (хотя с бурой и варится), вольфрам или молибден в этом плане лучше.
Вот здесь описание
about:reader?url=https%3A%2F%2Fworldweapon.info%2Ftenifer
Осталось понять где попаданцу взять металлы для легирования) Стоит отметить что цианат надо получать из мочевины отдельно, а потом использовать для цианирования. К тому же, если не ошибаюсь тенифер-процесс позволяет получать хоть и хорошое, но очень тонкое, порядка десятков микрон, покрытие. Так что на начальном этапе обычное цементирование полезнее. Это уже потом, когда речь пойдет о создании устойчивых к трению деталей и нарезных стволов, это будет актуально. Интересно как себя может показать комбинация этих двух методов, сначала цементацией получить слой в 2-3мм стали, а потом упрочнить его цианированием.
Железная руда — особенно магнетиты — очень часто содержат ощутимые количества хрома, марганца или титана, которые приивыплавке чугуна практически полностью переходят в чугун. В самостоятелтном виде минералы марганца и хрома тоже нельщя назвать редкими. Вольфрамит — частый спутник кассерита, тоже понятно где искать.
Цианат конечно лучше отдельно получать, чтобы не терять половину аммиака ищ мочевины, но можно мочевину и прямо в ванну добавлять до загрузки металла.
Тенифер покрытие действительно очень тонкое, но твердое, износостойкое и с антифрикционными свойствами. Совмещать с цементацией — смысла нет. Без закалки цементированная поверхность имеет низкую твердость, а закалка со стволом малосовместима по ряду причин.
Осталось попаданцу шлепнуться прямо на магнетитовую жилу, и желательно чтобы она залегала не на десятках/сотнях метров как КМА. Касситерит же настолько часто встречается что еще как финикийцы начали возить его аж с туманного Альбиона так и использовала его вся Европа, пока не открыли залежи в Африке и на Дальнем Востоке.
Магнетитовые пески встречаются достаточно шмроко (практически везде, где идет разрушение гранитов), и их с древноски использовали для получения железа. В Японии так это вообще основная железная руда была долгое время.
По ванадию, который тоже является нитридообразующим элементом:
Железные пески, которые добывали (и доьывают до сих пор) содержат 0.2-0.5% ванадия.
Новозеландские пески — около 0.6%.
В Индонезии — 0.7%.
На Камчатке, в песках Халактырского месторождения — вообще 1.2% (при 27% железа, т.е. даже до обогащения).
При выплавке чугуна весь ванадий переходит в металл (правда, он может в значительной мере выгореть при переделе на железо).
https://www.hitachi-metals.co.jp/e/tatara/nnp020603.htm
http://www.techhistory.co.nz/IronSands/Titanium.htm
ТЕХНОЛОГИЯ ПЕРЕРАБОТКИ ТИТАНОМАГНЕТИТОВЫХ ПЕСКОВ И РУД Коршунов Е.А., Буркин С.П.
https://www.youtube.com/watch?v=MDtJQcmb164
https://www.youtube.com/watch?v=ajOklIsfVf8
Два, на мой взгляд интересных ролика по обработке металла. Не совсем в тему статьи, но показывающий, что без уже существующего промышленного производства металлов (полностью сложившегося технологического процесса от добычи сырья до получения продукта с заданными свойствами)сложно говорить о каких-либо вменяемых масштабах изготовления изделий из металлов. Причем получение изделия с необходимыми механическими свойствами в принципе возможно, но чрезвычайно трудозатратно. А повторение технологического процесса (полученного опытным путем) практически невозможно из-за невозможности повторить необходимые условия. Даже полностью копируя рабочее место невозможно повторить все условия да и другой исполнитель будет вносит неопределённость. Технологию заново подбирать придётся.
Для получения цементованной стали в Англии использовалось шведское древесноугольное железо, известное как Oregrund или Dannemora (оба сорта из рудника Даннемора), стоило такое железо в XVIII в. около 21 фунта за английскую тонну.
Стоимость цементования (каменный уголь как топливо+древесный уголь как карбюризатор+зарплата рабочим) — от 1.5 до 2 фунтов за тонну стали, транспортировка еше 1 фунт. Готовая сталь продавалась по 26 фунтов, принося прибыль 3-5 фунта ща тонну.
Одну печь обслуживали 2 работника, при загрузке в 10 тонн или чуть больше и 12 загрузках в год производившие около 150 тонн стали в год.
Сталь из отборных кусков, собранная в пакет и проваренная под молотом несколько раз для гомогенизации, продавалась уже по 30-36 фунтов за тонну.
//The trade in oregrounds iron was controlled from the 1730s to the 1850s by a cartel of merchants, of whom the longest enduring members were the Sykes family of Hull. Other participants were resident in (or controlling imports through) London and Bristol. These merchants advanced money to Swedish exporting houses, which in turn advanced it to the ironmasters, thus buying up the output of the forges several years in advance//
Цементированная сталь, так же, как и сталь сырцовая, в исходном виде не годится для практического применения из-за неоднородности состава, и должна подвергуться гомогенизации. До появления тигельной стали такая гомогенизация приводилась хорошо известным с глубокой древности методом — кузнечной сваркой с последующим складыванием и новой проваркой. Так, если исходить из десятислойного пакета, то при простом удваивании (складывании пополам) семь операций сварки даст более 1000 слоев, что при толщине полосы с 50 мм соответствует толщине отдельного слоя порядка 50 микрон. При складывании, скажем, в пять раз такого же результата можно достичь за три операции проваривания.
Следует понимать, что помимо уменьшения толщины слоев и выравнивания состава на макроуровке идет процесс и на микроуровне, за счет диффузии углерода. При сварочной температуре (1100-1300 гр) скорость диффузии углерода в железе составляет порядка нескольких микрон в секунду, поэтому вместо теоретических сотен и тысяч слоев получается кусок стали с очень равномерныи распределением углерода (хотя и со множеством неметаллических включений шлака).
Поэтому две популярные точки зрения на древнюю сталь (первая — такая сталь жутко неоднородная, а вторая — такая сталь чудо композит из миллиона слоев) неверны.
Надо сказать, что существует способ действительно получить слои с сильно отличающимся свойствами — используя металл с повышенным содержанием фосфора, который даже в низких концентрациях сильно замедляет диффузию углерода и медленно диффундирует сам. Фосфористое железо часто использовали для ковки узорчатых мечей, однако только для наружных обкладок, на лезвие такой материал абсолютно не годился.
Что до современной узорчатой (дамасской) стали, в этом случае также не приходится говорить о чудесном композите с твердыми и мягкими слоями. Рисунок же, хорошо проявляющийся после травления, связан не с разным содержанием углерода, а с разным содержанием легирующих примесей — хрома, марганца и т.д., которые, в отличие от углерода, диффундируют с меньшей на порядки скоростью.
//Считалось, что получаемая, еще весьма высокоуглеродистая сырцовая сталь не годилась для выковки оружия, поскольку «…она местами или слишком груба, или слишком мягка. Притом же и не довольно чиста во внутренности, почему она должна быть улучшена.» Для улучшения брусковую сталь проковывали в ленты, затем закаливали и по излому разделяли на четыре сорта: твердую, среднюю, мягкую и негодную. Из 20-и листов первых трех сортов металла составляли пакеты, которые после первой сварки еще дважды разрубали пополам и сваривали, после чего расковывали на полосы. Такая 80-слойная сталь называлась «односварочною» и считалось годной не для оружия, а лишь для напильников и другого грубого инструмента.
Клинковую «двухвыварную» сталь получали своркой пакета еще раз отсортированных 20 лент «односварочной» стали с последующим окончательным удвоением и расковкой в бруски. Таким образом, златоустовская клинковая «сварочная сталь» состояла из 3200 слоев сырцовой стали, в свою очередь образованной сплавленной смесью частиц высоко, средне и малоуглеродистой составляющих.//
//logo
logoКаталог
logoКаталог
Поиск по сайту
Искать
СОРТОВОЙ И ФАСОННЫЙ ПРОКАТ
ТРУБЫ
ЛИСТ
СЕТКА
НЕРЖАВЕЮЩАЯ СТАЛЬ
ПРОВОЛОКА И МЕТИЗДЕЛИЯ
РЕЛЬС
АЛЮМИНИЙ
ЗАПОРНАЯ АРМАТУРА
ФИТИНГИ
КАЛИБРОВАННЫЙ ПРОКАТ
МЕДЬ
ЛАТУНЬ И БРОНЗА
ГНУТЫЕ ПРОФИЛИ
ЛЮКИ РЕВИЗИОННЫЕ
О компании
Металлоконструкции
Услуги
Контакты
Главная
Статьи
Старинные технологии металлов
Изготовление стальных и железных изделий
Изготовление стальных и железных изделий
Содержание материала
Изготовление стальных и железных изделий
Ковкое железо
Дамасская сталь
Нагрев стали
Все страницы
Диограмма содержания углеродаИзготовление стальных и железных изделий
Обшде принципы обработки железа; свариваше и паяние.
Свойства железа, важный для изготовлеюя изъ него изделий. Влияние содержания углерода.
Сырой материал доставляется на завод в одном из трех видов: въ виде чугуна, в виде стали или в виде железа. Химически чистое железо для промышленности пока никакого значения не имъет. Только углеродистое железо пригодно для изделий.
Съ содержаниемъ углерода примерно до 0,2% оно годно для кузнечныхъ подковъ и называется ковочнымъ железом. По мере повышешя содержали углерода железо становится в изломе все зернистее и зернистее. Примерно при 0,6% углерода металл приобретает способность при быстром охлаждении закаливаться — такой металл называютъ сталью. При увеличения содержашя углерода способность металла свариваться уменьшается, но зато увеличивается его плавкость. Мало углеродистое железо научились плавить сравнительно очень недавно, а сталь плавили уже давно. При увеличении содержания углерода до 11/2%—2% металл теряет способность коваться и свариваться. При дальнъйшемъ увеличении количества углерода металл становится все более и более легкоплавким; начиная с 3,5—5% углерода он называется чу-гуном. При быстромъ охлажденш закаливается (отбеливается) лишь поверхностный слой чугуна.Вышепоименованныя свойства металла изменяются очень сильно, если въ составь его введены хотя бы самыя незначительныя примеси другихъ элементовъ. Фосфоръ сообщаетъ чугуну жидкоплавкостъ, способствует отчетливому заполненю при отливке деталей формы, но уменьшаетъ крепость металла; железо и сталь отъ присутствия фосфора становятся хладноломки, т.-е. хрупкими на холоду; изломъ ихъ зернистее, чъмъ былъ бы безъ фосфора. Cеpa сообщаетъ металлу на холоду известную мягкость. Присутствие ее не мъшаетъ холодной обработка железа, но за то последнее становится красноломкимъ; оно совсемъ не годится для поковокъ и плохо выдерживаетъ сгибание въ горячемъ состоянии; марганецъ подобно углероду увеличиваетъ сопротивлете металла разрыву, но уменьшаетъ его вязкость. Твердость и мелкозернистость металла увеличивается также отъ введения въ составь его кремния, мышьяка, хрома, титана, молибдена и вольфрама; последний сильно увеличиваетъ и магнитность стали. Никкель получилъ въ новейшее время особое значение въ качестве примеси при изгото-
Диаграмма содержания углерода
влении броневыхъ плитъ, которым он сообщает большую твердость и вязкость.
Вышеупомянутый изменения свойствъ металла въ зависимости отъ со-держатя въ немъ углерода графически представлены на рис. 247. По горизонтальной линии отложены процентные содержания углерода, а по верти-кальнымъ соответственныя изменения ковкости, свариваемости, твердости, плавкости, сопротивления разрыву и вязкости. Разсмотримъ измънения ковкости (линия 1). Последняя очень велика при очень маломъ содержаши углерода и быстро понижается до нуля примерно при 2% углерода. Аналогично ковкости изменяется свариваемость (линия 2). Твердость (линияя 3), начиная съ 0,5% углерода, быстро увеличиваясь, достигаетъ максимальной величины при 2% его содержании; температура плавления очень высока въ начале, а по мере увеличения углерода понижается почти пропорционально содержанию
ПОСлеДНеГО.
Сопротивлете разрыву (линия 5), составляющее для ковкаго железа около 40 килр., повышается при 1% углерода до 1000 кил. и затемъ вновь быстро падаетъ.
Вязкость (линия 6), выражающаяся отношешемъ величины удлинешя куска металла передъ разрывомъ къ его длине, начинаясь съ 40% падаетъ до 6% при 11/2% углерода. Подробнее этот вопросъ разсматривается в металлургии. Различные сорта углеродистаго железа можно классифицировать следующим образомъ:
Сварочное железо — пудлинговое или кричное; литое железо — приготовленное на кисломъ или на основномъ поду въ Мартеновской печи или въ реторте Бессемера.
Сталь.
a) Изготовленная изъ чугуна
древесноугольная сырцовая сталь, приготовленная въ кричномъ горну; пудлинговая сталь.
b) Изготовленная изъ ковкаго железа
цементная сталь — приготовленная накаливаниемъ железныхъ полосъ съ уголънымъ порошкомъ.
Сталь, приготовленная по способу Дерби, т.-е. прибавлениемъ въ жидкое малоуглеродистое железо порошка кокса.
c) Изъ смеси чугуна и железа
Бессемеровская сталь, изготовленная прибавленемъ зеркальнаго чугуна въ Бессемеровскую реторту, после обезуглерожения ея содёржимаго.
Мартеновская сталь, приготовленная переплавкой железныхъ обрез-ковъ съ чугуномъ, на кисломъ или на основномъ поду.
Сталь Парри: приготовленная переплавкой въ вагранке железа и чугуна.Рафинированная сталь Сырцовая сталь, не играющая роли въ слесарномъ деле..
Сырцовая сталь страдаетъ отсутствиемъ равномерности и мелкозернистости, каковыя свойства она можетъ получить при раффи-нировании. Всякая сталь, полу-248. клещи. ченная въ жидкомъ состоянш или
нагретая до температуры, близкой къ ея температурь плавлешя, становится крупнозернистой и сравнительно мало прочной; проковкой и прокаткой можно придать ей мелкозернистость и увеличить ея прочное сопротивление. Раффинирование можно произвести: сваркой, совместной отливкой и совместной плавкой.
Для получения раффинированной стали сваркой приготовляютъ куски сырцовой стали, примерно 8 миллим. толщиной и 80 миллим. шириной, скла-дываютъ ихъ штукъ по 20 одинъ на другой въ пакетъ (рис. 248 а) и, подо-гревъ, проковываютъ подъ молотомъ. Сварка производится помощью многихъ повторныхъ подогревовъ. Обыкновенно полоса при этомъ такъ вытягивается, что становится удобнее разрезать ее пополамъ и обработывать каждую половину отдельно. Затемъ полосу перегибаютъ пополамъ (рис. 248 b) и опять свариваютъ такъ, что она состоитъ уже изъ 40 слоевъ. Далее снова продолжаютъ подогревать полосу и проковывать подъ молотомъ, снова перегибаютъ пополамъ и т. д., пока не получаютъ окончательно довольно равно-мернаго состава полосу — углеродъ стремится распределиться въ раскаленной полосе равномерно; это-то и есть излюбленная въ старину, раффиниро-вааная сталь. Вследств1е самаго происхождения она хорошо сваривается. Несмотря на всю ея видимую равномерность ее можно узнать потому, что въ горячемъ состояyии и при износе на ней выступаютъ следы полосъ, какъ это можно видеть на старинныхъ столовыхъ ножахъ и оружии, равнымъ обра-зомъ вследствие особенностей ея строешя острия изъ нея хорошо режут, ибо всегда слегка пилообразны, что на глазъ и незаметно. //
Сталь по методам получения
//(a) By modification of the conditions in the bloomery furnace such that some carbon was retained in the bloom and in this way producing NATURAL STEEL.
(b) By heating bloomery iron in a bed of charcoal under conditions such that carbon would diffuse into the iron. In early times such a process seems to have been confined to the treatment of finished articles so as to CASE НARDEN them.
(c) By enclosing small pieces of cast iron within layers of wrought iron sheet and heating them to a bright red heat (but short of fusion), out of contact with air, this being the CHINESE PROCESS.
(d) By melting cast iron in a crucible and immersing bars of wrought iron in the melt; in this way the iron bars absorbed carbon from the cast iron and after a while could be taken out and forged to give BRESCIAN STEEL.
(e) By applying the case hardening process to layers of bar iron, interspersed with powdered charcoal in large sealed chests, BLISTER STEEL could be made by the cementation process. The blister steel could then be broken into short lengths, these made into faggots and forge welded together to give SHEAR STEEL.
(f) By melting the cast iron and burning out just sufficient of the carbon by what was essentially a modification of the finery process to produce STYRIAN STEEL (which was also known as GERMAN STEEL and, most confusingly, was also referred to as NATURAL STEEL).
(g) By using a modification of the later puddling process and similarly burning out only sufficient carbon to produce steel, cast iron could be converted to PUDDLED STEEL.//
//Уклад, сырцовая сталь, которую получали из железной крицы. В русских летописях 16 в. упоминается У. новгородский, тихвинский, карельский и др. При нагреве крицы в раскалённом древесном угле происходило поверхностное науглероживание металла; в процессе охлаждения металла водой или снегом сталистый слой закаливался, становился хрупким и при ударе легко отделялся. Операцию повторяли до полного превращения крицы в листки. Наиболее крупные листки укладывали в раскалённые угли (отсюда название) и нагревали до сварки; раскалённая масса приобретала плотное строение. Из У. изготовляли холодное оружие, шлемы, серпы и т.д. С появлением пудлингования (конец 18 в.) и разработкой массовых способов получения литой стали (2-я половина 19 в.) У. потерял значение.
Лит.: Яковлев В. Б., Развитие способов производства сварочного железа в России, М., 1960.
Н. А. Мезенин.//
Надо отметить, достоверность этого описания вызывает некоторые сомнения. По крайней мере, в XVIII в укладом называли рафинированную многократным провариванием сырцовую сталь, получаемую кричным переделом.
А как эти листки «сваривали»? Судя по описанию, это, скорее, были чешуйки наподобие ржавчины или окалины.
Это к тому, что в теме про восстановление железа утверждалось про невозможность получения цельного куска из железного порошка. Вопрос: чем «сварка» стальных чешуек отличается от такой же «сварки» железных «опилок»?
Я и говорю, что достоверность именно этого описания вызывает сомнения.
Должны быть не чешуйки, а достаточно толстые, в пару мм пластинки из чего-то среднего между сталью и чугуном. Укладывали явно не просто на угли, а на железную пластину, с добавлениеи флюса. То есть примерно так же, как японскую таманэгане
http://www.ksky.ne.jp/~sumie99/forging.html
Вообще сварка небольших фрагментов железа (типа обсечек и обломков) в один цельный кусок всегда была достаточно рутинной операцией. В XIX в даже стволы охотничьих ружей сваривали из подковных гвоздей.
По поводу сварки именно мелкого порошка/опилок — тоже можно, но сильно сложней. Например, представим отражательную печь типа пудлинговой, в которой наводится ванна железистого шлака (от кричного горна, или песок плюс окалина или железная руда). В жидкий шлак закидывается порошок железа, все это перемешивается, слипается в крицу, которую затем нужно проковать.
именно так и пробовали делать, но без особого успеха, см. http://popadancev.net.s3-website-us-east-1.amazonaws.com/pryamoe-vosstanovlenie-zheleza/comment-page-1/#comment-166102