Фанера на первый взгляд кажется одним из первых кандидатов на производство попаданцу. Ведь всем известно, как делать фанеру! Вот цилиндр дерева (чурак), к нему подведен нож, чурак крутится и с него аккуратно сходят листы шпона, из которого можно выклеить массу полезных вещей, от римских щитов до корпусов аэропланов (в первую мировую некоторые самолеты так и выклеивали из шпона в бетонных формах-половинках, проклеивая листы банальным животным клеем и прижимая мешками с песком).
И возникает закономерный вопрос: почему тогда настоящая фанера появилась только в конце 19 века?!
Мои любимые воспоминания детства — визиты к деду в столярную мастерскую. Горы безумно вкусно пахнущей стружки, выше крыши зданий. Я брал и любовался здоровыми витками деревянных спиралек, покрытых снаружи зазубринками…
Стоп. Зазубринки.
Проблема в том, что когда нож свободно срезает стружку, она тут же ломается. Если строгать дерево вдоль волокон, то при определенных углах можно отщеплять без повреждений пластины шпона, потому что дерево вдоль волокон достаточно прочно и может выдержать изгиб, чтобы пропустить нож между основной массой заготовки и листом шпона. Однако лущильный станок должен резать поперек волокон.
Увы, при поперечном срезании снимаемое полотно шпона будет тут же ломаться, не отходя от кассы. Наверное, самым ярким примером этого явления будет заточка карандаша в точилке — выходящие из нее завитки дерева рассыпаются в порошок, и не только потому, что срез идет не параллельно волокнам.
При срезании с поверхности вращающегося цилиндрического тела слоя древесины и выпрямлении последнего в нем возникают внутренние напряжения: сжатия — на лицевой стороне и растяжения — на оборотной стороне. Так как прочность древесины на растяжение поперек волокон относительно невелика, при свободном резании перед режущей кромкой ножа образуется опережающая трещина, направление распространения которой произвольно, на поверхности шпона неизбежно появятся еще и большие микронеровности (выступы на оборотной стороне, углубления — на лицевой).
Таким образом, если лущить только с применением ножа, получить качественный шпон невозможно.
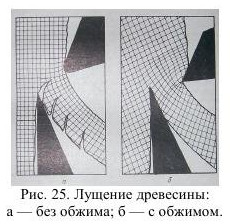
Выходом из положения является сжатие древесины в зоне внедрения в нее ножа, что достигается специальным прижимным органом, устанавливаемым около ножа на расстоянии меньшем, чем толщина шпона (т. е. подача суппорта на один оборот чурака). Он создает зону сжатия, простирающуюся по радиусу в глубь чурака. Уплотнение древесины в непосредственной близости от прижимного органа достигает 30—40 %. При срезании ножом слоя древесины и прохождении его между передней гранью ножа и прижимным органом происходит сжатие слоя в радиальном направлении.
Дальше начинается весьма непростая задача — обеспечить точную подачу прижимного органа (это может быть или клиновидная пластина металла или цилиндр, причем цилиндр, несмотря на трение качения, требует больших усилий на прижим). И точное расположение прижимного органа относительно ножа. Все эти параметры надо или считать по давно выведенным формулам, или самому исследовать вовсе с нуля.
Другой проблемой является точный выбор угла резания. А он меняется, зараза, с уменьшением диаметра чурака. Для компенсации чего у лущильных станков имеется не только горизонтальная подача, но и механизм изменения наклона ножа.
А теперь задумайтесь, смогли ли бы вы разобраться в физике данного явления без интернета, в деревенской мастерской и до того, как инвестор вас на конюшне запорет за невыполненные обещания?
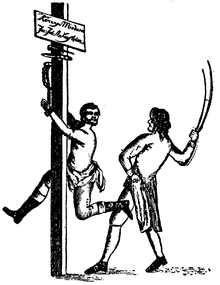
Хорошая статья.
Благодарносте
Еще есть такой эффект как то что прочность древесине придает био-полимер Лигнин. Если нагреть его до 100 градусов и немного влажности, то полимер этот станет мягким и мять древесину становиться намного легче. Скорее всего и раскатать бревно на шпон тоже будет легче. Основное ограничение было не в мозгах (умне и сообразительные есть всегда и везде), а в социальной структуре общества.
Если нагреть его до 100 градусов и немного влажности, то полимер этот станет мягким и мять древесину становиться намного легче.
Распаривание бревен — стандартная операция при лущении. Она не заменяет сжатия древесины при лущении, без этого вы никогда не получите приличного шпона.
Эх, а что ж про распаривание не написали. Распаривать, наверное, тоже нужно уметь определенным образом. И не только при лущении. Есть видео, где деревяшку распаривают, сжимают в тисах, а затем пропихивают в разные непропихиваемые места.
Для полного описания процесса надо брать учебник какой-нибудь, там много всего прочего, кроме распаривания.
напишите ссылку на учебник
А сейчас такие станки без электроники выпускают? Спасибо.
Интересно, а как этот вопрос решали на первых станках? Куча микрометрических винтов и хитрых передач?
Зачем куча? один единственный винт устанавливающий толщину шпона (т.е. зазор между прижимом и ножем) и пара рычагов которые ось прижима сдвигают по мере опускания ножа.
Нож соответсвенно, закреплен на длинном рычаге что позволяет игнорировать дугообразность траектории.
/
/
╱╱┏╮
╱╱┃┃
▉━╯┗━╮
▉┈┈┈┈┃
▉╮┈┈┈┃
╱╰━━━╯
Отличная статья! Спасибо!
Вспоминается резорцин-формалиновая смола, которой можно не только хорошо клеить фанеру, но и пломбировать корни зубов, причём ещё не ясно, что будет выгоднее.
Получается смешиванием формалина и резорцина, которые можно получить оттуда же, откуда и фанеру — срубив под корень ближайший лес. Сухой перегонкой древесины можно получить метанол, который после пропускания его над медным или серебряным катализатором превращается в формалин. Резорцин получают расплавив смолу деревьев с калиевой щёлочью или простой перегонкой смолы, если повезло с сортом дерева. Смесь застывает красным густым клейким веществом.
Также найдя эвгенол (содержится в масле гвоздики в больших количествах, а также в мирте и эвкалипте) можно сделать примитивную местную анестезию и цемент, смешав гвоздичное масло с порошком оксида цинка. Если уж добыли оксид цинка, то достав оксид магния и фосфорную кислоту можно сделать ещё и фосфатный цемент. Применив ещё немного смекалки, ртуть, серебро и золото, можно теперь делать серебряные пломбы и золотые коронки, клеить их на цемент или смолу, пломбировать корни и зубы. При наличии желающих деньги потекут рекой.
Впрочем, можно этой смолой и фанеру клеить. Смола устойчива к воде и УФ-излучению, можно склеить корпус корабля из фанеры.
интересный вопрос в догонку, шпон известен достаточно давно, как его делали до изобретения станка? или тогда это был шпон вдоль волокон?
Два вида:
пиленый шпон, т.е. тонкие пласты отпиленные поперек волокон и обточенные на наждаке до приемлемой плоскости.
колотый шпон- т.е. лущеный вдоль волокон с плоской прямослойной заготовки.
И то и другое известно со времен древнего мира, мебель с мозаичными элементами из шпона и покрытие дешевой древесины шпоном дорогих сортов делалось еще в древнем Риме.
Недостатки обеих технологий в сравнении с лущильным станком- маленькая площадь отдельных кусочков шпона и большое число отходов в случае пиленого.
/Сухой перегонкой древесины можно получить метанол, который после пропускания его над медным или серебряным катализатором превращается в формалин./
про метанол и формалин здесь есть отдельные статьи
/Получается смешиванием формалина и резорцина/
да не просто так смешением. Без рН метра, вискозиметра и термометра сложно. Да и с ними, если сам не варил, на так просто.
По резорцину — не проще ли фенол (не помню, но вроде про него тоже есть статья)
Ну вот и ответ любителям построить планер из древне-римской фанеры!
Глупости говоришь. Я всегда утверждал что фанера планеру не нужна. С ней конечно проще но и без нее обойтись можно.
Кроме того, кроме лущеного шпона есть еще колотый (т.е. лущеный с плоской а не с цилиндрической заготовки) и пиленый. Правда их крупными листами не получить. Но на важные узлы, если вдруг возникнет желание, изготовить всегда можно.
Ну и текстолит на казеине делает фанеру совсем уж ненужной роскошью.
собственно в статье не подняты еще два вопроса каким клеем склеивать фанеру? сейчас это карбамидный клей и фенол-фармальдегидная смола. Соответственно вопрос: как и когда можно получить этот клей и есть ли нормальные древние аналоги? Ну и вопрос, для производств фанеры все равно понадобится пресс и смолы, и тогда вопрос может имеет смысл сразу перешагнуть технологию и сразу делать ОСП плиты? Сделать стружечному-щепочный станок проще?
собственно в статье не подняты еще два вопроса каким клеем склеивать фанеру?
«нельзя объять необъятное» (c)
Соответственно вопрос: как и когда можно получить этот клей и есть ли нормальные древние аналоги?
Вся эта химия далеко за пределами возможностей одного человека. А самое поганое, к этим клеям прилагается еще и гигантский горячий пресс.
Ну и вопрос, для производств фанеры все равно понадобится пресс и смолы, и тогда вопрос может имеет смысл сразу перешагнуть технологию и сразу делать ОСП плиты?
ОСП — это не улучшенная фанера, это утилизация древесных отходов. Если у вас есть горы стружек и остатков древесины от производства чего-то еще, это хороший бонус, но не более того.
OSB (как и ДСП) не утилизация отходов. Это специальное оборудование, которое и производит стружку (разную для ДСП, МДФ и OSB)
ну собственно мы и уперлись в главные вопросы современной фанеры — влагостойкие клеи и горячие прессы хороших размеров.
«А теперь задумайтесь, смогли ли бы вы разобраться в физике данного явления без интернета, в деревенской мастерской и до того, как инвестор вас на конюшне запорет за невыполненные обещания?»
Никто не требует для отработки технологии сразу строить дорогую полноразмерную модель 🙂 для экспериментов по круговой лущильной машине для представления инвесторам достаточно создать прототип который будет лущить 10 сантиметровые чураки, которые можно распарить и дома в большой кастрюле и сделать модель с ручным приводом, и нож и и прижимной механизм и винтовую регулировочную схему можно составить не в деревне конечно, но в приличной городской мастерской с конца 16 века точно (аналоги по сложности изготовления это токарные станки для дерева). Вопрос в другом, а нужна ли фанера в это время кому то для массового производства? Боюсь что такой материал никому особо не нужен будет. Фанера это массовый материал, но я не вижу кому он может пригодиться при таком массовом производстве :). Представим попадает попадает с устаревшей фанерной фабрикой пусть там будет все автономно и своя плотина с маленькой электростанцией и весь заводик и все для изготовления, пусть даже с персоналом заводика он попадет. Материал только подвози. И вот пользуясь что все есть, наделал он фанеры и приехал показывать ее в Питер или Лондон. Его там и спросят ну и че? и на фига она нужна, доски дешевле и лучше. Может разве что иконописца заинтересуются, но спрос то мизерный :)… Материал то будет, рынка сбыта не будет, придется заниматься пропагандой того, для чего она нужна. 🙂
для экспериментов по круговой лущильной машине для представления инвесторам достаточно создать прототип который будет лущить 10 сантиметровые чураки
Нет.
На малой модели вы никак не увидите те глюки, которые у вас вылезут на полноценном станке в этом деле. Кроме того, лущить чураки малого диаметра до сих пор является мега-проблемой, и до сих пор остаются достаточно толстые «карандаши» после лущения, идущие в отходы. Задача уменьшения диаметра остающихся «карандашей» до сих пор остро стоит. У вас и на малой модели ничего толком не получится, и она ничем не поможет в создании нормального станка.
Фанера это массовый материал, но я не вижу кому он может пригодиться при таком массовом производстве
Это уже совсем другой вопрос 🙂
Собственно, цель данной статьи — показать, что в даже простых на первый взгляд и привычных технологиях есть мелочи, не зная которых вы получите абсолютно не то, что ожидали. Не более того.
А так, в принципе, фанера в доогнестрельную как эрзац-доспехи и щиты для ополчения, почему нет? Но для этого хватит и лущеной вдоль, с помощью длинного рычага с лезвием. Жаль, потерял ссылку на видео, на котором старый финн шпон строгал такой штукой, а теперь найти не могу.
Никотин писал про чурбаки ДЛИННОЙ 10 см, а не диаметром. Чтобы нож не делать слишком длинным, чтобы усилие резания было маленьким… для демонстрации сойдет и даже что то можно изготавливать для продажи выложив плоскость из нескольких лент.
Размер остаточных «карандашей» практически не имеет значения, фанера НАМНОГО дороже чем деревяшки. т.е. даже при 50% отходах стоимость сырья многократно меньше дохода.
Используется фанера прежде всего мебельщиками и каретниками. Тонкий, прочный и упругий материал позволяет сделать просторную, легкую карету, которую свободно тащит пара лошадей вместо тяжеленного и узкого деревянного гроба который с трудом волочет шестерка.
Фанерный шкаф с гнутыми стенками намного изящнее и проще в изготовлении чем тяжелый досчатый.
Так же фанера легко найдет потребителя в строительстве (легкие РОВНЫЕ!!! перегородки без щелей, потолки).
А смысл в лущении лент сложным станком, когда ленты можно налущить вдоль — и качественнее и примитивным рычагом? Ась?
Это не будет той прочной фанерой, к которой мы привыкли.
Сколько пойдет в отвал не важно, важно то, что на маленькой модели вы нифига не решите то, с чем столкнетесь на большой.
И кстати, казеиновая фанера в карете — очень плохая идея. Ибо загниет и развалится через полгода, после чего см. последнюю картинку с попаданцем.
«А смысл в лущении лент сложным станком,» — отработка технологии точки и усилия прижимного клина и отладка механизма наклона ножа и винтовой регулировки в зависимости от диаметра. 🙂
«Фанерный шкаф с гнутыми стенками намного изящнее и проще в изготовлении чем тяжелый досчатый.»— Давайте посмотрим когда появился массовый спрос на мебель? тогда и нашлось применение фанере, а до этого шкафы, это вотчина краснодеревщиков, которые изготовляли штучную мебель для очень ограниченного класса людей. :). То же самое и со строительством. Для богатых фанера не выглядит богато, а для бедных она дорога. Проще и надежнее доски.
Каретное дело? Пожалуй соглашусь, но придется очень морочится с защитой от влаги, и покрывать дорогостоящими лаками. Боюсь для карет знати пойдет, а для массового продукта нет.
Так что до внедрения аэропланов боюсь, что спроса не будет. Но статья хорошая!!!
//Каретное дело? Пожалуй соглашусь, но придется очень морочится с защитой от влаги, и покрывать дорогостоящими лаками.
Если обратить внимание на дошедшие до наших дней кареты, то они все были крашенными и лакированными. Да я и не представляю, как кто-то поедет в некрашеной деревяхе? Так что в этом пункте, трудоемкость изготовления никак не изменится. А вот вес кареты явно уменьшится. Как и скорость изготовления.
Так что, даже небольшой станок вполне может окупиться. Ведь для кареты не требуются полотна 7,7 на 1,55 метра. И даже 2,4 на 1,2 не требуются.
К тому же, в связи с тем, что для обработки фанеры не требуется краснодеревщик высшей квалификации, то на лицо сильное снижение стоимости произведенной мебели. Как за счет ЗП мастера более низкой квалификации, так и просто за счет увеличения скорости производства работ. Что как раз открывает рынок для среднего класса. К тому же, фанера все еще недоступна беднякам, и это является дополнительным отличительным фактором для недомажоров 🙂
//А смысл в лущении лент сложным станком, когда ленты можно налущить вдоль — и качественнее и примитивным рычагом? Ась?
Да ну? Сможете ленту длинной метров 10 налущить вдоль?
впрочем главное в этом станочке отработка технологии и демонстрация заказчику дабы вложил денег на полноразмерный вариант. Всех проблем на маленькой модели не решить но блоьшинство отладить удастся.
//Это не будет той прочной фанерой, к которой мы привыкли.
зато намного прочнее и однороднее того к чему привык абориген-заказчик 🙂
//казеиновая фанера в карете — очень плохая идея.
Подсказываю: казеин с льняным маслом. Прочно и влагостойко.
Ну а чтоб не гнила древесина (в любой форме) кареты красят или лаком покрывают.
//Давайте посмотрим когда появился массовый спрос на мебель?
Он был всегда. Не всегда у потребителя были деньги. Купцы и ремесленники в городе с удовольствием купят красивый шкаф «прям как у господ», но на работу краснодеревщика их доходов не хватит. Фанерная мебель это массовый продукт для среднего класса.
Разумеется верхний слой фанеры может быть и из дорогого шпона. Так (дорогой шпон на дешевое дерево) делали еще в Древнем Риме.
//Боюсь для карет знати пойдет, а для массового продукта нет.
ну собственно карета она у знати только и есть, держать выезд удовольствие дорогое. Но кареты для извозчиков в больших городах это тоже огромный рынок.
«Но кареты для извозчиков в больших городах это тоже огромный рынок»
давайте посмотри когда появились извозчики в больших городах, и массовые купцы и ремесленники. 🙂 . Лущильный станок это 1810 год, а формирование массовой прослойки среднего класса, которая и потребляет услуги извозчиков, да массовую мебель — это 1775 год примерно, хотя многие поспорят и скажут что не ранее 1790 года. Нет средний класс был и до этого, но численность его…. если вас устроит продавать на париж или питер 1500 листов фанеры в год, то явно овчинка выделки не стоит. 🙂
хм… купцы даже во времена Петра первого представлены в количестве. В те годы «первая сотня» уже давно перестала быть именно сотней т.е. на любой средний город (а это от одной до 30 тысяч) имеем несколько сотен человек среднего класса плюс практически у каждого из них приказчики и помощники которые тоже скорее всего относятся к среднему классу.
Сюда же владельцы мастерских, мастера и подмастерья.
Добавим сюда старших чиновников (младшие в средний класс не попадают) и дворян.
А так же частично слуги дворян (горничную средним классом не назовешь, а вот дворецкого у городского главы бедняком назвать сложно…).
т.е. де факто городские жители (которых конечно всего пару процентов от общего числа жителей) процентов на 10-30 состоят из среднего класса.
Да и остальные жители города в большинстве своем вынуждены использовать услуги извозчика ибо своего выезда у них нет. Это не деревня, где у каждого есть лошадь, ведь без нее пахать невозможно, разве что у соседа одолжить.
Если вспомнить книги 18, 19 веков то извозчиками пользовались и студенты и чиновники.
Так что кареты извозчиков (кэбы, пролетки и т.д.) весьма популярная и массовая продукция.
Да и дилижансы из фанеры легче и просторнее выйдут.
Ну а на счет востребованности… с XVII века в москве был Тележный ряд который позже был переименован в Каретный. А рядом с ним большой, малый и средний каретные переулки. Четыре улицы длинной в пару километров где были сосредоточены мастерские по производству телег и прочих транспортных средств. Вот настолько невостребованны были кареты и пролетки в Москве несколько веков назад.
/ сразу перешагнуть технологию и сразу делать ОСП плиты?/
Вас не смущает, что они появились значительно позже фанеры а даже ДСП и ИДФ?
МДФ выше, ошибся
По поводу клея — там в самом первом абзаце статьи написано про животный клей. Клей надо подбирать в зависимости от технологии — пресс холодный или горячий, мешки с песком или металлические плиты с хорошим давлением и т.п. А еще важна водостойкость, или нет. Это сильно меняет дело.
на всякий случай напоминаю, что понятие водостойкость весьма относительно и нуждается в привязке к условиям эксплуатации
Непонятно где и когда это применимо.
Если до 18 века, то неприменимо ибо в каждом городе свои «цеховые братства» всяких мебельщиков/каретников и тп. Они вас с камнем привязанным к ногам выкинут в ближайшую реку.
Никаких конкурентов тогда не терпели, рынок маленький и он окучивается всегда одними и теми же людьми и сам рынок не растёт.
Если только создать влагостойкую фанеру и начать делать какие нить лодки/баржи.
По поводу предварительного сдавливания перед резанием — В ютюбе полно видео с японскими рубанками, там дяди снимают буквально миллиметровый слой вдоль всей доски метров 5-7. тупо ручным острозаточенным рубанком.
И что они потом из этого слоя делают? Явно не для дешевых табуреток корячатся.
http://glavmex.ru/forum/download/file.php?id=6995&sid=1eb82fe99b126a9f80f8af1d8ba6dec6
Есть вариант попроще лущильно -роторный станок.
он есть в этой теме.
http://glavmex.ru/forum/viewtopic.php?f=16&t=7277
На промышленных предприятиях, т.н. «фанерках» древесину перед роспуском на шпон выдерживают в горячих бассейнах 80С и выше до суток (зимой), бассейны тоже не маленькие, с такой хорошеньких размеров стадион, брёвна прижимают плитами, над всем этим парком бассейнов ходят козловые или мостовые краны. Вонищща стоит…. Но это на крупном предприятии и лущат на шпон сосну, иногда по спецзаказу — листвяк. Как с берёзой и осиной обстоит дело — могу только предположить.
Для нужд попаданца, во всяком случае на первых порах, чурбаки нужны будут около метра, не больше, древесина — как-раз лиственных пород, может даже быть какая полегче, например липа или кедр. Получит листы в 1 кв.м., склеенные каким-либо спиртовым клеем(водостойкие) или овсянным (рисовым/пшеничным/рыбным/костным/сам придумай….) клейстером (требуют гидроизоляции, но для мебели вполне пригодны), склеит/сколотит из них карету или «ероплан и улететь на… из етого колхозу»
Станок изобретен еще в 1851, и фанера не была так уж популярна и необходима в самолетостроении
// “in 1851, when Immanuel Nobel, father of Alfred Nobel, the inventor of dynamite and benefactor of the eponymously, if ironically, named Peace Prize, patented an effective rotary lathe. A log is mounted at both ends in this huge machine tool and spun around while a long knife is applied all along its ”
“length, cutting through and unraveling a thin sheet of veneer, like a sheet of toilet paper being unwound from a roll. The technique requires the log to be almost perfectly straight, but for the first time this meant that huge sheets of veneer could be produced. At first, the quality of plywood made from these veneers was poor because the animal and plant glues that were used to stick the veneers together were not waterproof and tended to rot. Plywood was largely limited to internal use and for simple items such as artists’ boards for oil painting. But furniture designers soon found it to be an ideal material. Designers such as John Henry Belter of New York showed that it could readily be bent and molded into two-dimensional, and even three-dimensional, curves, enabling him to produce graceful rococo revival furniture.”
…
“In World War I, which followed soon after, though, the plywood design was only taken up by a few German designers. Small numbers of beautiful Roland C.II “Walfisch” reconnaissance aircraft, my personal favorite, and the Albatros D.V fighter were built, and they looked great, the front of the fuselage often being painted with the jaws of sharks, to emphasize their sleekness and ferocity. However, they were outnumbered by planes with the traditional braced wood frame.”
“slightly higher weight of these aircraft or their tendency to rot in wet weather.”
…
“In the 1920s the waterproofing problem was finally overcome by gluing the veneers together with new polymer-based resins.”
…
“plywood made a dramatic comeback in World War II. Worried by shortages of metals, British aircraft designers developed cheap wooden gliders for airborne assaults such as the Normandy landings, and even a superfast bomber. Nicknamed the Wooden Wonder by its crews, the de Havilland Mosquito had a fuselage made using an ingenious sandwich construction, in which a light central core of balsa was covered on each side by three-ply birch plywood”
Насчёт фанеры и казеина.
Встречалось что на ПМВ в России существовало только одно предприятие по выпуску авиационной фанеры на казеина, в Риге. И продукция разбегалась чуть ли не с дракой потребителей.