Вероятно, многие слышали слово «тиокол». Кто-то вспомнит жидкость с омерзительным запахом, которую добавляли в эпоксидный клей для увеличения эластичности. Кто-то припомнит разбирательства после катастрофы «Челленджера» в 1986 г, причиной которой стал твердотопливный ускоритель производства компании Мортон-Тиокол. Чем же тиоколы могут быть полезны попаланцу?
Все началось в 1926 году, когда американские химики Джозеф Патрик и Натан Мнукин занимались разработкой антифризов. Когда они попытались получить сернистый аналог этиленгликоля из дихлорэтана и полисульфида натрия, вместо этого получили резиноподобную массу, которая забила раковину и при попытках растворить ее оказалась устойчива ко всем растворителям, находившимся в лаборатории. Поскольку искусственный каучук, да еще устойчивый к бензину, был в то время своего рода священным граалем для химиков, исследования были продолжены и в 1929 г была основана компания Тиокол. Справедливости ради нужно упомянуть, что образование резиноподобного вещества из дихлорэтана и полисульфидов химики наблюдали еще в середине XIX в., но тогда этому не придали никакого внимания.
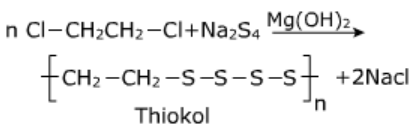
Первый продукт, известный как тиокол А (на основе дихлорэтана и тетрасульфида натрия), пытались использовать в автомобильных шинах, но не успешно — такие шины изнашивались в несколько раз быстрее, чем из натурального каучука, кроме того, переработка тиокола (например, горячее вальцевание) сопровождалось отвратительно пахнущими испарениями (хотя и малотоксичными). Затем в 1930-х были разработаны жидкие тиоколы, способные отверждаться при комнатной температуре, которые сразу нашли применение как герметики в авиации и судостроении и оказавшиеся идеальным связующим для первых смесевых порохов для твердотопливных ракет и ускорителей. Но вскоре были найдены лучшие материалы и для бензостойких шлангов, и для ракетного топлива, тиоколы же остались в качестве достаточно нишевых продуктов, и в таком виде применяются до сих пор.
Привлекательность полисульфидных каучуков для попаданца состоит в легкости их получения и в весьма неплохой комбинации свойств. Исходные полисульфиды легко готовятся кипячением или сплавлением карбонатов или гидроксидов натрия или калия с порошком серы, причем длина полисульфидного фрагмента задается простым соотношением реагентов. Дихлорэтан легко получается из этилена и хлора. А сам каучук образуется в водном растворе при смешивании обоих компонентов. Простые полисульфидные каучуки, типа тиокола А, гораздо менее эластичны и износостойки, чем натуральный каучук, и дубеют на морозе (что решается использованием более длинных полисульфидных мостиков, или же других дихлоридов, тоже легко доступных даже попаданцу), но зато очень химически устойчивы к бензину, маслам и многим растворителям, не чувствительны к свету и кислороду (даже к озону), имеют прекрасные диэлектрические свойства. Полисульфидные каучуки имеют очень низкую газопроницаемость, натуральный каучук же пропускает воздух почти как решето.
Жидкие тиоколы можно получить, обрабатывая тиоколовый каучук раствором сульфита натрия при кипячении. В этом случае полисульфидные связи рвутся, и получается смесь олигомеров с -SH группами на конце. Если такой тиокол смешать с диоксидом свинца PbO2, суриком Pd3O4 или диоксидом марганца MnO2, то концевые группы окисляются в мостики -S-S-, и опять получается твердый каучук, причем отверждение происходит практически без усадки. Отверждать жидкие тиоколы можно и без добавки оксидов металлов, за счет атмосферного кислорода, но для этого требуется длительное время, порядка нескольких недель. Возможностей применения жидких полисульфидных каучуков для попаданца еще больше — кроме связующего для ракетного топлива или пороха такие тиоколы отлично подходят для прорезиненных тканей и шлангов.
Компания Тиокол же кроме полисульфидных каучуков разработала много различных продуктов в области полимеров, а также активно занималась разработкой и производством ракет на твердом топливе. Причиной катастрофы «Челленджера» стал твердотопливный ускоритель, разработанный фирмой Мортон-Тиокол, в котором произошел прорыв газов через уплотнительные кольца из витона (фторированного каучука), потерявших эластичность при запуске в слишком холодную погоду.
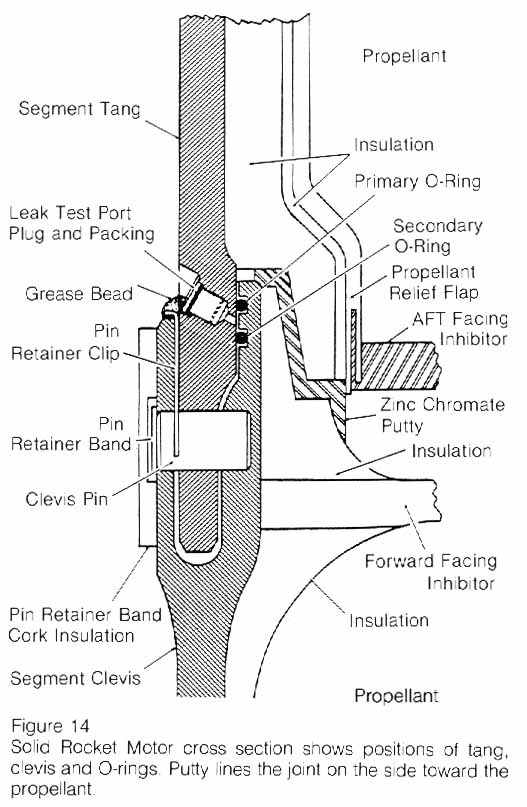
Тиокола как материала в этих ускорителях, возможно, вообще не было.
Немного невнятно про получение. Вернее писал химик для химика и стараясь охватить максимально широкий спектр вариантов.
Лучше взять пару-тройку конкретных вариантов, например «эластичный», «прочный», «жидкий» и разобрать конкретное получение, т.е. берем едкий натр и порошок серы, в соотношении х:у кипятим, в полученную жидкость добавляем дихлорэтан, фильтруем выпавший осадок…
Как то так…
Может, немного спутанно получилось, но детали зависят от многих факторов, хотя бы от того, что есть в распоряжении попаданца — сода, поташ, или едкий натр? По-моему, тут достаточно понимания, что: а). Полисульфидный каучук крайне просто сделать, лишь бы сера не в дефиците была и хоть какое-то производство хлора было организовано и б). На основе такого каучука можно изготовить крайне полезные материалы — например, прорезиненную ткань. Частности придется на месте выяснять, но при общем понимании сути процесса можно в адекватное время уложиться.
// что есть в распоряжении попаданца — сода, поташ, или едкий натр
хотя бы вариант для самого простого — поташа
На самом деле действительно сложно понять (не химику). Прекрасно понимаю вариативность процесса, но все же хотелось бы понять последовательность действий с нуля, от получения исходных компонентов до конечного материала. «…Обычный способ получения полисульфидных каучуков состоит в обработке дихлорэтана полисульфидом натрия в водном растворе щелочи. Полученную водную дисперсию тиокола промывают водой (декантацией), после чего проводят коагуляцию минеральной кислотой…»
Т.е. необходимо получить дихлорэтан, полисульфид натрия и раствор щелочи.
1. С щелочью понятно — поташ.
2. Полисульфид натрия — получают сплавлением сульфида натрия с серой. Сульфид натрия получают прокаливанием мирабилита (Na2SO4 · 10H2O.). Мирабилит получают действием серной кислоты на хлорид натрия или находят в природе на высохших соленых озерах. Вот здесь уже вопросы (не химика)))), хлорид натрия — (составная часть морской соли), мирабилит (тоже составная часть морской соли), как их разделять или необязательно? Или получается залить серную кислоту в морскую соль? — сомневаюсь что-то. Или прокалить морскую соль? тоже как то… Опять же только мирабилит или непринципиально какой сульфид 10-водный или 1-водный.
3. Дихлорэтан. Получают пропусканием хлора через этилен. Этилен получат смешиванием спирта и серной кислоты с нагревом. Хлор получают электролизом из раствора соли.
Я правильно процесс понял ?
По-моему, поташ — это не очевидно. Например, если хлор производится электролизом, то исходить нужно из гидроксида натрия.
Если же нет, то лучше полисульфиды получать из сульфата натрия (отход производства соли из морской воды или подземных рассолов, http://popadancev.net.s3-website-us-east-1.amazonaws.com/gradirovanie/#comment-153335), который при прокаливании с углем превращается в Na2S. Растворение серы в растворе Na2S опять же приведет к полисульфиду. И в первом, и во втором случае нужно ориентироваться на получение тетрасульфида (соотношение натрия к сере 1:2), но если серы будет в 1.5-2 раза больше, тоже сойдет.
Если же сульфат натрия получать искуственно, из соли и серной кислоты, то образующийся хлороводород можно использовать доя получения дихлоргидрина (пропускание газообразного хлороводорода через нагретую до 100 гр смесь глицерина и уксусной кислоты). Дихлоргидрин заменяет дихлорэтан, так что можно даже без хлора обойтись, и все необходимое сырье ограничивпется серой, глицерином и солью.
Спасибо ))) Вот это прям развернутый, подробной ответ, понятный даже мне ))).
Надо, наверно, определиться с временнЫм интервалом полезности введения попаданцем этого тиокола,хотя бы примерно
Если попаланец строит генератор и есть сера — то когда угодно. При большом желании можно и без генератора. Вопрос в реальной необходимости, что, в общем-то, и для обычного каучука применимо.
//А. В трехгорлой колбе, емкостью 500 мл, снабженной мешалкой, обратным холодильником, термометром и капельной воронкой, растворяют 38,4 г (0,40 моля) сульфида натрия (моногидрата) в 150 мл воды. К раствору добавляют 37,5 г (1,17 моля) серы и смесь нагревают до кипения в течение 1 часа с перемешиванием. К этому раствору в течение 1 часа при перемешивании приливают 40 г (0,40 моля) дихлорэтана при 70°. Темно-красный цвет раствора полисульфида исчезает только при добавлении последних порций дихлорэтана. Реакционную смесь нагревают при 70° еще 1 час, затем дают охладиться и верхний жидкий слой декантируют с желтого каучукоподобного твердого продукта, который трижды промывают кипящей водой. После высушивания над фосфорным ангидридом в вакуум-эксикаторе выход полимера 50-54 г (79-86%). Полагают, что очень неприятный запах продукта обусловлен присутствием низкомолекулярных дитиолов или циклических дисульфидов. Сероуглерод вызывает набухание и частично растворяет полимер, четыреххлористый углерод и бензол вызывают набухание полимера в той же степени. Температура плавления полимера на горячем бруске около 130°.
Б. Чтобы приготовить описанный выше полимер в более легко обрабатываемой измельченной форме, полимеризацию проводят в присутствии суспензии гидроокиси магния [60]. Последовательность операций реакции А изменяется добавлением к раствору тетрасульфида натрия 8,5 г (0,04 моля), хлорида магния (гексагидрата) и 3,6 г едкого натра перед самым добавлением дихлорэтана. Добавление диспергирующего агента, например натриевой соли алкилнафталинсульфоновой кислоты, в количестве 5 г ускоряет реакцию нерастворимого в воде дихлорида. Конденсацию проводят, как и в реакции А. при энергичном перемешивании. По завершении реакции частички полимера отстаиваются в течение 2 час, и верхний слой декантируют. Полимер повторно диспергируют в воде перемешиванием и снова отделяют от промывной жидкости. Эту операцию повторяют дважды, чтобы удалить неорганические соли. Центрифугирование ускоряет процесс промывки. Для некоторых целей дисперсия полимера в воде является удобной формой при переработке. Для коагуляции полимера в латекс можно добавить при перемешивании 10 мл концентрированной соляной кислоты, Губчатый каучуко-подобный желтоватый полимер выделяют и сушат в вакуум-эксикаторе, как описано выше.//
Неочевиден, прежде всего, дихлорэтан. Про хлор статья есть, но и там все не так просто (если не считать электролиз) а этилен откуда — из этанола и серной кислоты?
Кроме дихлорэтана подойдет дихлоргидрин (см. ниже) — даже хлор не нужен, только хлороводород.
Про этилен статья вроде тоже есть, спирта достаточно.
Применение — большой вопрос.
Дирижабли? Шланги для ранних ДВС?
Т.е. это конец 19 — начало 20го веков.
Раньше такой дубовый, непрочный и чуть что — вонючий каучук вряд ли пригодится — для одежды и т.п. любой растительный будет лучше и, вероятно, дешевле. Да и на отверждённых маслах водостойкость получить, пожалуй, лучше будет.
Т.е. это специализированный каучук индустриальной эпохи.
Т.е. и синтез надо ориентировать на соответствующее время, а не «из угля и воды в каменном веке».
Применение — хотя бы прорезиненная ткань.
Растительный конечно лучше, но он вовсе не везде есть, и в чем-то даже тиоколу проигрывает. Хотя бы в атмосферостойкости — резина из НК, особенно до XX в (без антиокислителей) за пару месяцев на солнце придет в негодность. А воздух в тонком слое пропускает как решето.
Да и вообще тиоколы не такие уж и хреновые по механическим свойствам
//П. к. усиливаются активными наполнителями и из-за наличия функциональных групп способны вулканизоваться оксидами Zn, Mg, Pb с получением резин прочностью 7–10 МПа и относит. удлинением 150–400%//
Даже для шин попаданцу вполне подойдут — если будет что обувать в шины
На ткань вряд ли.
Растительный «хоть какой-то» есть почти везде (те же одуванчики — по цене труда крестьян в сравнении трудом алхимиков :)).
Непроницаемость для воздуха — для одежды скорее минус.
Сравнивать с резиной без антиоксидантов смысла нет — если есть попаданец, то уж их в альтернативу добавить сообразит.
А вот апгрэйд тиокола «активными наполнителями» по мне так менее тривиален.
На ранние шины — ОК, если НК или бутадиеновый (т.е. спиртовой) почему-то дефицитен.
Но в любом случае — это материал индустриальной эпохи.
И, кстати, не сказал бы что синтез бутадиенового так уж сложнее, тут скорее по ресурсной базе выбирать.
Дирижабли, пневма, ДВС в дизельпанке — его ниша :).
Диэлектрики — само собой, но альтернатив там хватает.
Кораблестроение?.. Ну если сидеть на месторождении серы и каких-то масличных культур под глицерин — может быть. Но всё равно очень дорого в до-индустриале, соотношение цена-эффект сомнительное. И если есть большое кораблестроение — то и за гевеей сплавать не так сложно, однако ж не заморачивались в РИ этим.
//На ткань вряд ли//
На ткань самое то
//Непроницаемость для воздуха — для одежды скорее минус//
Особенно для дождевиков, сапогов, гидрокостюмов — нуну…
//если есть попаданец, то уж их в альтернативу добавить сообразит//
Еще на месяц-три срок службы продлит, не больше.
//апгрэйд тиокола «активными наполнителями» по мне так менее тривиален//
вы, очевидно, не в курсе, но в практически любую резину добавляют активные наполнители — сажу обычную и белую, окись цинка и т.д. Без них прочность и износостойкость в 3-5 раз меньше.
//Ну если сидеть на месторождении серы и каких-то масличных культур под глицерин//
Древний Рим — серы под Неаполем полно, масла тоже.
> //Непроницаемость для воздуха — для одежды скорее минус//
> Особенно для дождевиков, сапогов, гидрокостюмов — нуну…
Для одежды нужна водонепроницаемость, а вот газо- и паропроницаемость наоборот желательны.
Другое дело, что в реально водонепроницаемом — и эти проницаемости пренебрежимы даже в современных материалах.
> //если есть попаданец, то уж их в альтернативу добавить сообразит//
> Еще на месяц-три срок службы продлит, не больше.
Обоснуя не вижу. Даже описания объекта и условий, для которых «рассчитаны» эти «месяц-три», и выбранного антиоксиданта :).
> //апгрэйд тиокола «активными наполнителями» по мне так менее тривиален//
> вы, очевидно, не в курсе, но в практически любую резину добавляют активные наполнители
Я, очевидно, в курсе. Как и того, что подобрать оптимальные наполнители на механические и термические свойства — задачка куда более сложная, чем просто антиоксиданты. Тупо целевых параметров больше. Да и просто дисперсные наполнители почти всегда более сложный объект в оптимизации, чем растворимые.
Или Вы доказываете, что «с сажей и т.п. обычно лучше чем без них»? Если да, то кому? 🙂
> Древний Рим — серы под Неаполем полно, масла тоже.
Как вариант. А «полно» — это тысячи легкодобываемых тонн, или что там в наличии по сере?
//пренебрежимы даже в современных материалах//
Ну и к чему тогда рассуждения о необходимости воздухопроницаемости?
//Обоснуя не вижу//
Я тоже. Если считаете, что найти подходящий антиоксилант так легко, да еще и совместимый с каучуком, то и обосновывайте.
//задачка куда более сложая//
Если отойти от теоретизирования — как раз наоборот. Хотя бы потому, что результат сразу виден, а не через месяц.
//тысячи легкодобываемых тонн//
Именно, и не только около Неаполя, но и на соседней Сицилии.
> Ну и к чему тогда рассуждения о необходимости воздухопроницаемости?
Так это у Вас рассуждения о том, что она недопустима в одежде :). Я утверждаю, что этого ограничения нет, и воздухопроницаемость как минимум не вредит.
> Если считаете, что найти подходящий антиоксилант так легко, да еще и совместимый с каучуком, то и обосновывайте.
Ну, это Вы выдали прогноз с сроками. Не припоминаю, чтобы писал про «так легко», а что «легче» — таки да. Даже в древности можно на растительных полифенолах или дёгте попробовать. Сюрпризы будут обязательно, но с наполнителями их будет больше — система сложнее.
> Если отойти от теоретизирования — как раз наоборот. Хотя бы потому, что результат сразу виден, а не через месяц.
Учитывая «доступность» реагентов и логистику — даже дополнительный месяц для серии экспериментов погоды не сделает от слова совсем. А вот куча дополнительных параметров — таки да. И откуда мысль, что «результат сразу виден»? Свежеполимеризованный полимер от прошедшего старение отличается изрядно. Можно старить искусственно, но это и сейчас нетривиально правильно сделать. Дисперсные компоненты, кстати, и к свету/окислению сенсибилизировать могут — и это тоже надо проверять. Так что…
И насчёт теоретизирования — я с наполнителями (коллоиды и углеродные усы) как раз работал практически, адгезию к матрицам менял и анизотропную ориентацию делал. А вы на какую практику ссылаетесь?
//Так это у Вас рассуждения о том, что она недопустима в одежде//
Не пытайтесь мне приписать то, чего я не утверждал. Это как раз вы пытались привести воздухонепроницаемость как недостаток.
//растительных полифенолах//
Как обычно, никакой конкретики. Хоть один пример растительного полифенола, совместимого с вулканизированной рещиной?
//А вы на какую практику ссылаетесь//
Разработка материалов, в том числе и наполненных.
> //Так это у Вас рассуждения о том, что она недопустима в одежде//
> Не пытайтесь мне приписать то, чего я не утверждал. Это как раз вы пытались привести воздухонепроницаемость как недостаток.
Цитирую:
Вы: ///Применение — хотя бы прорезиненная ткань.
Растительный конечно лучше, но он вовсе не везде есть, и в чем-то даже тиоколу проигрывает. Хотя бы в атмосферостойкости — резина из НК, особенно до XX в (без антиокислителей) за пару месяцев на солнце придет в негодность. А воздух в тонком слое пропускает как решето.
Я: //Непроницаемость для воздуха — для одежды скорее минус//
Вы: Особенно для дождевиков, сапогов, гидрокостюмов — нуну… »
> //растительных полифенолах//
> Как обычно, никакой конкретики. Хоть один пример растительного полифенола, совместимого с вулканизированной рещиной?
Надеюсь, ещё и экспериментальной проверки не потребуется? 🙂
А так — извольте, этерифицированный и/или олигомеризованный таннин. А может и просто таннин подойдёт.
Похоже, вы или между строчек читать умеете, или просто додумывпете недостающие слова.
Про одежду я вообще не упоминал, прорезиненная ткань это не только дождевички (для низ и воска или олифы хватит).
По антиоксидантам — опять двадцать пять. Вы серьезно считаете, что таннин, даже «этерефицированеый и олигомеризованный», будет в каучуке и резине растворим и срвместим? У меня лично есть пара идей толковых антиоксидантов, просто хотелось ваше мнение узнать.
> Похоже, вы или между строчек читать умеете, или просто додумывпете недостающие слова.
Про одежду я вообще не упоминал, прорезиненная ткань это не только дождевички (для низ и воска или олифы хватит).
Ну, учитывая, что Вы отвечали на нижеприведённое сообщение:
«Раньше такой дубовый, непрочный и чуть что — вонючий каучук вряд ли пригодится — для одежды и т.п. любой растительный будет лучше и, вероятно, дешевле. Да и на отверждённых маслах водостойкость получить, пожалуй, лучше будет.»
— мне представлялось очевидным, что за ткань имелась ввиду. Тем более, что про дирижабли я отдельно писал. Но если нет — то нет :).
А насчёт «приписывания и додумывания» — так где это я утверждал что воздухонепроницаемость «недопустима в одежде»? 🙂
> Вы серьезно считаете, что таннин, даже «этерефицированеый и олигомеризованный», будет в каучуке и резине растворим и срвместим?
Что ему помешает? С cтеариновыми хвостами, например. Более того… допускаю, что таннином и сшивать можно — при отсутствии серы. Да и с фурфуролом его любопытно подружить.
Да, тио соединения как антиоксиданты очевиднее — но у них совсем другая (не растительная) ресурсная база. Аллилитиол из чеснока прошу не предлагать 🙂
Хоспаде, ну что за срачь про одежку?
Я так понимаю получится что-то вроде макинтоша? https://ru.wikipedia.org/wiki/%D0%9C%D0%B0%D0%BA%D0%B8%D0%BD%D1%82%D0%BE%D1%88_(%D0%BE%D0%B4%D0%B5%D0%B6%D0%B4%D0%B0)
Отличная вешь, пользовалась успехом, несмотря на недостатки.
Применение — кораблестроение. Герметизация швов. Возможно полностью покрытие корпуса прорезиненной тканью. Может показаться, что я зациклен на этом направлении. Но до появления железных дорог, водный транспорт единственный адекватный способ перемещения грузов и людей на значительные расстояния. А стратегические ресурсы не находятся в одном месте. Их транспортировать необходимо и в больших объемах. Так что вопрос логистики просто жизненно важен. И все сопутствующие технологии. Реальная история показывает что возможно создавать достаточно большие и мореходные суда но для их производства необходимы высокие требования к материалам и мастерству изготовления. Современные технологии позволяют значительно снизить требования как к первому так и ко второму. Да и применение как диэлектрика интересно. Так что и в «каменном веке» условно конечно («бронзовый» так точно), но имеет место быть.
Для герметизации швов и смолы хватит. А как диэлектрик — да, даже сейчас применяют
Смола — «герметик» от безысходности. Желательно искать замену. Конечно можно и на смоле сделать, но тут, еще раз говорю высокие требования к качеству древесины и изготовления. Необходимо подбирать материал с равной выдержкой, чтобы при набухании от воды равномерное расширение происходило и зазоры равномерно расходились. Подгонка при сборке ну очень точной должна быть. Смола не всегда ошибки сборки могла исправить. Течь и так все равно была, но иногда прям критично. Если вместо просмолённой пакли использовать резиновую прокладку уже намного проще. А если покрывать прорезиненной тканью так вообще красота.
А механические св-ва у этой штуки какие? В качестве пружин на огнестреле юзать можно?
В качестве пружин точно не подойдет, и эластичность не та, и остаточная деформация большая.
Лично, честно говоря, только в эпоксидку добавлял (клей-компаунд к-153).
Из самых очевидных начальных применений: оплетка провода, одежда (особенно обувь и подошвы для неё!), палатки, лёгкие быстросборные суда (лодки, плоты, понтоны), шланги (!), те же ласты (где-то здесь есть тема о невозможности их изготовления без резины) и маски, гибкие ёмкости для воды (те же вёдра) и дофига чего ещё.
Всё с двойным применением, т.е. интересно как для армии, так и гражданских.
Лёгкость приготовления и вариативность характеристик позволяют внедрить широкое кустарное производство буквально в каждой деревне. Или мануфактуру в каждом городе.
Топливо для ракет на тиоколовой связке
https://www.angelfire.com/planet/rubber-rocket/thiokol-rubber-fuel.html
http://www.astronautix.com/s/solid.html