Во многих областях чугун просто незаменим, и внедрять его выплавку стоит как можно раньше, тем более что принципиальных сложностей для этого нет практически в любую эпоху.
Обычный серый чугун хорошо подходит для отливки деталей машин и станков, посуды, а благодаря стойкости к перепадам температуры и химической стойкости — для сосудов и труб на химическом производстве.
Основной недостаток серого чугуна состоит в хрупкости, поскольку углерод в нем находится в виде пластинчатых графитовых включений, что способствует росту и распространению трещин.
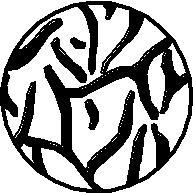
Но свойства чугуна можно кардинально улучшить, меняя морфологию графита и получая в результате ковкий или высокопрочный чугун.
Для КЧ и ВЧ в первую очередь необходим подходящий состав исходного сплава. Он должен быть низкоуглеродистым (2.5-3.5% C), и содержать минимальные количества серы и фосфора, не более 0.1-0.2%. Кремний и марганец в больших количествах тоже нежелательны. Отличный вариант исходного сырья — древесноугольный чугун из небольшой домны без подогрева воздуха, тем более именно такую домну построить проще всего. Имеет смысл и получение синтетического чугуна науглероживанием кричного железа в тиглях при 1200-1400 градусах — так даже из самой плохой руды вполне можно выплавить металл, свободный от нежелательных примесей.
Для получения ковкого чугуна нужно сначала сделать отливку из белого чугуна, в которой весь углерод находится в форме цементита Fe3C (этому способствует низкое содержание кремния и фосфора, а также быстрое охлаждение отливки). Превращение белого чугуна в ковкий происходит в процессе длительного, в течение 10-25 часов, отжига при 950-1000 градусах (закалка исходного белого чугуна сокращает это время до 5-7 часов за счет образования центров графитизации), при этом цементит распадается и углерод выделяется в виде графита, но не пластинчатой, как в СЧ, а хлопьевидной формы, оказывающей значительно меньшее ослабляющее влияние.
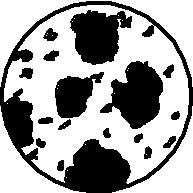
Структура самой железной матрицы зависит от режима дальнейшей обработки — при медленном охлаждении получается перлитный КЧ; если же охладить отливку до 700-750 и выдержать при этой температуре еще несколько часов — ферритный КЧ.
В результате формируется материал с пределом прочности на растяжение около 300-400 МПа и предельным удлинением 12-3% (для ферритных и перлитных КЧ соответственно). По сравнению с 150-200 МПа и <1% , типичных для СЧ, разница колоссальная.
Еще более радикальное улучшение механических свойств чугуна происходит при модифицировании расплавленного чугуна присадками магния, кальция, церия и др. Присадки вводятся в малых количествах, 0.1-0.3%, и служат инициаторами для выделения графита в виде сферических частиц прямо при охлаждении расплава.
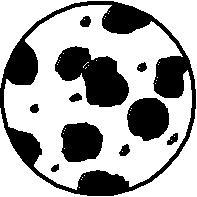
Поэтому не нужен длительный отжиг, а свойства получающихся высокопрочных чугунов приближаются к среднеуглеродистым сталям — предел прочности 500 МПа и выше (до 1000 МПа), удлинение 10-20%. К тому же ВЧ хорошо заполняет формы при отливке и имеет маленькую усадку.
И КЧ, и ВЧ могут подвергаться термообработке (закалка, отпуск), что еще больше расширяет область их применимости.
И когда такой чугун начали использовать? Rupertino cannons?
Стоили втрое дороже обычных, но треть из этой цены была уплата по патенту
// the high cost of the gun—three times the price of a regular weapon … The guns cost £60 per ton as Rupert received a royalty of £20 per ton
Тут еще почему-то обкладывают железом
// Réaumur conducted extensive research on malleable iron in 1720. He discovered that iron castings which were too hard to be worked could be softened by packing them into iron ore or hammer slag and exposing them to high temperature for a number of days.
Насколько я понимаю, суррогат литой стали? Не такая высокая температура плавления, но и не такой прочный.
//И когда такой чугун начали использовать?// ковкий — еще китайцы. А широко внедрили только в XIX в в Европе. Высокопрочный — в середине XX в.
Пушки Руперта лили из серого чугуна, отжиг в первую очередь для снятия напряжений, и, возможно, для перевода металла в ферритную форму и размельчения графита. Дефекты типа отбела поверхности при этом тоже должны были ликвидироваться, графитизацией как в КЧ. Основная добавка в цене, имхо, это мехобработка наружней прверхности — за счет нее даже при криво установленном литьевом стержне получалался равностенный ствол. Еще лучше отливать без канала, и полностью высверливать центр отливки со всеми литьевыми дефектами.
//обкладывают железом//
Не железом, а оксидами железа. Это обратная цементация или адуксирование, опять же использовалась китайцами для массового производства инструментов — лемехов, топоров, ножей и т.д. В заметке про цементацию железа упоминалась в конце.
ВЧ не просто суррогат стали, с учетом хороших литейных качеств изделия из него могут быть даже лучше стальной отливки.
Тема интересная. Из чугуна можно сделать много чего. Но тяжёлая промышленность такая тяжёлая.
(первая мысоль, из чугуна можно желать отличные пушки).
А если развить тему, что ещё можно сделать из чугуна, чтобы было востребованной?
Посуда? Но тут годится обычный чугун, ковкий особых преимуществ не даёт. Детали машин и механизмов — для внутреннего пользования попаданца. Так и вижу чугунный паровой котел.
Чугун будет дешевле стали, и изтнего удобно делать литые детали. это главный плюс.
//Посуда? Но тут годится обычный чугун, ковкий особых преимуществ не даёт//
Ковкий чугун тут имеет большие преимущества, он не треснет от случайного удара, а стенки можно делать тоньше.
Отжиг на ковкий чугун может быть просто вынужденной мерой — низкокремнистый и низкофосфористый чугун застывает в белой форме, очень твердой и хрупкой. Именно поэтому в Европе чугун дрлгое время и не находил применения. Можно или добавить фосфора (костной золы) при выплавке, что улучшит литейные свойства и ухудшит мех. свойства серого чугуна, или выполнить графитизующий отжиг и получить ковкий чугун. Что лучше — зависит от конкретного случая
Ножи, топоры и т.п. из ковкого чугуна делать можно?
Кстати вопрос а будет ли хорошей идеей получать сталь путём прокаливания полос стали с оксидом железа или железной стружкой в тиглеле. Так сказать совместить воедино 3 техпроцесса из последних статей.
Я знаю что это изврат и проще тот же оксид железа или стружку спекать напрямую с углеродом но тут могут возникнуть проблемы с качеством продукции. Плюс куски углерода могут застрять в крице и ее придется тщательно проковывать.
А так имея чугун стабильного состава мы можем получить очень стабильные по составу полосы не нуждающиеся в долгой кузнечной обработке. При желании из них можно делать ножи или мечи ну или стволы мушкетов. Можно даже отливать сразу стволы, прокаливать, выпрямлять и протачивать. Должно получится лучше и дешевле чем из крицы.
//полос стали с оксидом железа //
Полос чугуна имелось в виду? Именно сталь с определенным содержанием углерода так получить сложно, сложно контролировать. Мягкое железо можно, но качество вряд ли лучше кричного будет — в металле останутся все примеси, а структура получится зернистой. На стволы вряд ли сойдет, для менее ответственных деталей — вполне.
А чем вам не нравиться много раз прокованый дамаск? Так называемый «цыганский дамаск»?
Цыганский дамаск, как понимаю, это сварочная сталь, науглероживаемая в процессе сварки порошком чугуна. По сути материал очень похожий на аналогичные сварочные стали — уклад, тамахаганэ и т.д.
А можно ли легировать чугун калием?
Насчет калия информации нет. Кипит он при 750. Разве что как раскислитель.
Хорошая статья!
Но тема не раскрыта в принципе — легкий обзор вышел.
Ковкий чугун интересно сравнить с бронзой — например, БрО10 (10% олова, примерно из такого сплава пушки отливали) имеет предел прочности при растяжении 215-275 МПа, удлинение 3-10%. Ковкий чугун имеет 290-360 МПа при той же пластичности 7-12%, и заметно легче (7000 вместо 8800 кг/м3).
Учитывая, что из бронзы делали не только пушки, но и стволы пистолетов и мушкетонов, ковкий и тем более высокопрочный чугун должны вполне подойти для этих же целей.
Смущает простота метода по описанию с статье.
Высокопрочный чугун я подозреваю сообще не для попаданца
// Ductile cast iron
// Tiny amounts of 0.02 to 0.1% magnesium, and only 0.02 to 0.04% cerium added to these alloys slow the growth of graphite precipitates by bonding to the edges of the graphite planes.
По поводу хлопьев
https://web.a.ebscohost.com/abstract?direct=true&profile=ehost&scope=site&authtype=crawler&jrnl=05779170&AN=37216673&h=Acys%2bl%2benmJS94ohWjd3faKighTdw6OnIig2lXPLlewTxaHHGL8VNLViFxNjH5FKtTZq4YCaCioYWB06gccQew%3d%3d&crl=c&resultNs=AdminWebAuth&resultLocal=ErrCrlNotAuth&crlhashurl=login.aspx%3fdirect%3dtrue%26profile%3dehost%26scope%3dsite%26authtype%3dcrawler%26jrnl%3d05779170%26AN%3d37216673
// The Chinese cannon bodies were largely cast in white iron, while the British ones were mostly cast in gray iron. Secondly, the shapes of graphite in the gray iron composition show some differences. In the Chinese cannons, the graphite is mostly in the form of flakes; however, in the British cannons, the graphite has two forms (75% flakes, 25% flowers). Flower-shaped graphite provides for better-quality gray iron. In addition, Britain had better casting and processing technologies. As a result of these factors, British cannons from the Opium War were of better quality than Chinese ones, and this, in turn, affected British performance.
THERMAL STABILITY OF CAST and WROUGHT MARINE IRON. Studies in Conservation, 21(4), 192–197. doi:10.1179/sic.1976.030
серый чугун с хлопьями графита — по крайней мере с 17 века
В общем как я понимаю пушечный чугун и так был с хлопьями, только и благодаря кремнию и благодаря медленному охлаждению
grey cast iron
Silicon is important for making grey iron as opposed to white cast iron, because silicon is a graphite stabilizing element in cast iron, which means it helps the alloy produce graphite instead of iron carbides; at 3% silicon almost no carbon is held in chemical form as iron carbide. Another factor affecting graphitization is the solidification rate; the slower the rate, the greater the time for the carbon to diffuse and accumulate into graphite. A moderate cooling rate forms a more pearlitic matrix, while a fast cooling rate forms a more ferritic matrix. To achieve a fully ferritic matrix the alloy must be annealed
//Высокопрочный чугун я подозреваю сообще не для попаданца//
Почему же? Там достаточно ОДНОГО магния. Поскольку магний кипит ниже температуры литья чугуна, сильно окисляется и реагирует с серой, то его берется порядка 0.2-0.5%, чтобы в итоге осталось 0.05-0.1%. То есть всего 2-5 кг магния на 1 тонну чугуна, хотя, конечно, лучше не в чистом виде, а в сплаве с кремнием (который тоже придется восстанавливать из песка магнием, еще ~5 кг).
Редкоземельные металлы — опционально, а не обязательно.
Более серьезная сложность — относительно высокая температура литья, ~1400 градусов. Не 1700, как для стали, но тоже не мало.
//In 1947, British H. Morrogh found that addition of cerium in the hypereutectic gray cast iron, and when the content of cerium is more than 0.02wt%, the graphite was spherical. In 1948, American A.P.Ganganebin et al. researched and pointed out that addition of magnesium in the cast iron, then addition of silicon iron alloy for inoculating, when the residual magnesium is more than 0.04wt%, the graphite is spherical too.//
Тут подробнее https://web.archive.org/web/20041214102034/http://moderncasting.com/archive/feature_023_01.html
На родине слонов, похоже, сами додумались
//В тоже время мы имеем данные, о том, что термин «высокопрочный чугун (с шаровидным графитом)» постоянно стал использоваться в советской конструкторской и спецпрофильной документации с середины 1937 года.//
//В 1946 году был издан ГОСТ 3443-46 «Отливки из серого и высокопрочного чугунов. Структура и методы её определения». Это говорит о том, что уже к 1945 году в Советском Союзе ВЧШГ был хорошо известен как материал для использования в различных сферах народного хозяйства.//
Возможно, это домыслы, слово высокопрочный в 57 г добавили, гост 46 г в полном варианте найти не получается.
//серый чугун с хлопьями графита — по крайней мере с 17 века//
Вас ввело в заблуждение несоответствие терминов на разных языках. Пластинчатый графит на английском как раз flake или lamellar, хлопьевидный — compacted и flower-like, шаровидный — nodular и spherical, червеобразный -vermucullar.
Все эти определения достаточно условны, и есть много переходных форм.
Тем не менее чугунные пушки — это именно серый чугун, имеющий очень маленькое предельное удлинение 1% и менее. Кремний как раз способствует выпадению пластинчатого графита.
Ковкий чугун, технология которого разработана Ледебуром в XIX в. (хотя что то подобное иногда получалось и раньше), разрывается при удлинении на 5% и выше.
На английском ковкий чугун разделяется на две категории — Whiteheart malleable cast iron (иначе адуксированный чугун), про который упоминалось в заметке про цементацию, и blackheart malleable cast iron, который собственно и соответствует ковкому чугуну в русскоязычном варианте.
Вот тут подробней
https://www.giessereilexikon.com/en/foundry-lexicon/Encyclopedia/show/malleable-cast-iron-4435/?cHash=8663a1e5e2389625bbe1a98bb8f2a8ba
https://www.totalmateria.com/page.aspx?ID=CheckArticle&site=kts&NM=96
Ок, с такими дополнениями дело выглядит интереснее.
полуоффтоп — а как насчет фришевания? процесс очень напоминает восхваляемый конвертер
// Однако для широкого рас-
пространения доменной плавки в качестве основного ма-
нуфактурного способа производства железных изделий
необходимо было разработать технологию передела чугуна
в ковкий металл. Такая технология была создана во второй
половине XVI в. в Бельгии и получила название «фришева-
ние», т.е. «оздоровление» (или очистка) чугуна. Фришева-
ние быстро распространилось на предприятиях Англии, а
затем Швеции и других европейских стран.
Сущность фришевания заключалась в окислении при-
месей чугуна в струе воздушного дутья в ходе плавления
и стекания капель чугуна по древесному углю. При этом
из чугуна последовательно удалялись кремний, марганец,
фосфор и углерод. По мере удаления из металла углерода
он переходил в тестообразное состояние, и в результате
на поду печи формировалась крица с небольшим количе-
ством шлака, источником которого служили окисленные
примеси чугуна и зола древесного угля. Поэтому крицу
тщательно проковывали.
Так фришевание — это кричный передел, в Китае его уже с III в. использовали, в Европе с XIV-XV в., причем этот метод был основным до XIX в., в России — до последней четверти XIX в., а в Швеции последнее производство остановили аж в 1960-х. Каждый метод передела (старонемецкий, штирийский, валлонский, контуазский и т.д.) заточен под местные условия, конкретное сырье и т.д. Потенциал для модернизации, имхо, нулевой.
Если руды и древесного угля в достатке, а железо нужно в ограниченных объемах, то хватит сыродутных методов; если нет — то сразу пудлингование или более продвинутые методы уже нужно внедрять.
Некоторые детали технологии модифицирования чугуна
//Обязательным при производстве отливок из высокопрочного чугуна является модифицирование с целью получения шаровидного графита, низкое содержание серы (менее 0,012 %) при отсутствии в химическом составе демодификаторов (Вi, Sе, А1, Тi, Аs, Pb).//
//Для первичной сфероизидирующей обработки чугуна используют металлический магний, лигатуры и смеси, содержащие щелочноземельные и редкоземельные металлы//
//В отличие от металлического магния многокомпонентные сплавы-сфероидизаторы (лигатуры) позволяют существенно упростить и удешевить процесс модифицирования, целенаправленно управлять структурообразованием и свойствами ЧШГ, а также снизить пораженность отливок литейными дефектами.
Самыми распространенными являются модификаторы на основе магния, в частности лигатуры магния с ферросилицием ФСМг, а также лигатуры Ni–Si–Mg, ЖКМК (Fe–Si–Mg–Са) и КМ (Si–Са–Mg). Для модифицирования используют также редкоземельные металлы (РЗМ – Lа, Се, Nd и др.).//
//Для формирования в структуре шаровидного графита необходимо, чтобы количество усвоенного модификатора соответствовало 0,03…0,06 %. При меньшем количестве образуется не шаровидный, а пластинчатый графит, при большем появляется отбел, т. е. возникает необходимость в термической обработке//
//Сэндвич-метод. Это наиболее широко используемый метод в массовом производстве автомобильных отливок из ЧШГ. Он предусматривает размещение мелкокускового магнийсодержащего сплава-сфероидизатора в углублении донной части футеровки ковша, нанесение на всю открытую поверхность сфероидизатора слоя покровного материала (обычно стальных штамповочных высечек). Ковш заполняется жидким чугуном таким образом, чтобы струя расплава не попадала прямо на лигатуру и покровный материал.
+ Основные преимущества сэндвич-процесса: простота, низкая себестоимость, технологическая гибкость. Основные недостатки: значительные дымовыделения (оксид магния) и свечение, сопровождающие обработку; относительно низкое, иногда нестабильное усвоение магния (обычно 30—40 %); значительное увеличение содержания кремния в чугуне, что ограничивает количество оборотного скрапа ЧШГ, который может быть переплавлен, и содержание кремния в исходном чугуне; значительное снижение температуры чугуна при обработке;//
//МДС-проиесс (предложен ЦНИИТМАШ). Модифицирующая смесь засыпается в разогретый до 600-800 °С ковш не ранее 5 мин до выпуска металла. Необходимое количество модифицирующей смеси определяется в зависимости от содержания серы в исходном чугуне и составляет обычно до 0,1 % магния от массы обрабатываемого чугуна. При повторении цикла модифицирования в ковше не должно быть остатков жидкого чугуна. Выплавка чугуна для модифицирования может производиться в любых плавильных агрегатах (вагранка, дуговая или индукционная электропечь). Химический состав исходного чугуна должен соответствовать составу требуемой марки ЧШГ. Температура чугуна перед модифицированием должна быть в пределах 1320-1460 С. Модифицирование чугуна начинается с момента выпуска его в ковш из плавильного агрегата. Сливать чугун в ковш следует с максимально возможной скоростью, направляя струю металла в свободный от модификатора карман. При случайном попадании струи металла в карман с модификатором происходит вспышка магния в результате перемешивания струей модифицирующей смеси, которая всплывает в чугуне и за несколько секунд сгорает на поверхности чугуна. В этом случае модифицирование следует считать неудачным, металл должен быть слит в печь. Нормально процесс модифицирования сопровождается кипением металла, интенсивным его перемешиванием без выплесков и пироэффекта. При окончании процесса кипение прекращается Продолжительность модифицирования в ковшах емкостью от 0,5 до 5т составляет от одной до трех минут. Технология МДС — процесса считается экономичной для небольших литейных производств, отличается высокой стабильностью и гибкостью процесса, позволяет получать ЧШГ с высокими прочностными и пластическими свойствами в литом состоянии как при выплавке чугуна в электропечах, так и в вагранках//
//Для целей лабораторных и исследовательских работ, а также при небольших объемах производства предпочтителен способ ввода модификатора под колокольчиком в ковше с металлической крышкой (рис.1, а). В шамотографитовый или стальной колокольчик 1 с отверстиями в боковых стенках закладывают бумажный пакет с навеской модификатора. Пакет закрепляют в колокольчике вязальной проволокой. Крышку 2 надевают на штангу колокольчика и устанавливают на ковш. Колокольчик опускают в глубь металла.//
//Жидкотекучесть высокопрочного чугуна выше, чем жидкотекучесть серого чугуна, поэтому тонкостенные отливки высокопрочного чугуна получаются без проблем. Усадочные свойства в значительной степени зависят от литой структуры отливки. Если отливка затвердевает «по-белому», то в ней образуются усадочные раковины и необходимы прибыли, как и для белого чугуна. Объем усадочных дефектов достигает 6% и более; возникают горячие и холодные трещины. Если структура высокопрочного чугуна получается в литом состоянии (как правило, при использовании вторичного модифицирования ферросилицием), т.е. при затвердевании не выделялся структурно свободный цементит, а происходила графитизация, то объем прибылей и объем усадочных дефектов уменьшается на 20… 30 % и составляет 4,5… 5,5 %. Горячих трещин при этом не возникает, холодные трещины образуются реже, чем при затвердевании «по-белому»//
//Из других технологических свойств следует прежде всего отметить более высокую герметичность высокопрочных чугунов из-за отсутствия графитной пористости, и эти чугуны можно использовать для отливки деталей, работающих при давлениях 40 МПа (400 кгс/см2) и выше//
//По металлической матрице чугуны подразделяются на ферритные, перлитно-ферритные, перлитные и бейнитные. Чугуны первых двух типов производят в литом состоянии без термической обработки, перлитные чугуны получают с нормализацией, а бейнитные — с закалкой и отпуском//
Китайские вагранки для плавления чугуна с верхним дутьем
https://dl.dropboxusercontent.com/s/a45jx75lfx572bf/%D0%B2%D0%B0%D0%B3%D1%80%D0%B0%D0%BD%D0%BA%D0%B0%20%D1%81%20%D0%B2%D0%B5%D1%80%D1%85%D0%BD%D0%B8%D0%BC%20%D0%B4%D1%83%D1%82%D1%8C%D0%B5%D0%BC%201.png?dl=0
https://dl.dropboxusercontent.com/s/uxneq9g6r77uoeo/%D0%B2%D0%B0%D0%B3%D1%80%D0%B0%D0%BD%D0%BA%D0%B0%20%D1%81%20%D0%B2%D0%B5%D1%80%D1%85%D0%BD%D0%B8%D0%BC%20%D0%B4%D1%83%D1%82%D1%8C%D0%B5%D0%BC%202.png?dl=0
Микроскопическая китайская домна с производительностью около тонны в день
https://dl.dropboxusercontent.com/s/5ho9q19p4yc6mw4/%D0%BC%D0%B0%D0%BB%D0%B5%D0%BD%D1%8C%D0%BA%D0%B0%D1%8F%20%D0%B4%D0%BE%D0%BC%D0%BD%D0%B0%20%D1%84%D0%BE%D1%82%D0%BE.png?dl=0
https://dl.dropboxusercontent.com/s/z4t0hlvw6n36fld/%D0%BC%D0%B0%D0%BB%D0%B5%D0%BD%D1%8C%D0%BA%D0%B0%D1%8F%20%D0%B4%D0%BE%D0%BC%D0%BD%D0%B0%20%D1%81%D1%85%D0%B5%D0%BC%D0%B0.png?dl=0
https://dl.dropboxusercontent.com/s/6obx47wa780qy0t/%D0%BC%D0%B0%D0%BB%D0%B5%D0%BD%D1%8C%D0%BA%D0%B0%D1%8F%20%D0%B4%D0%BE%D0%BC%D0%BD%D0%B0%20%D1%87%D0%B5%D1%80%D1%82%D0%B5%D0%B6.png?dl=0
//The fuel used was charcoal, and blast was provided by a traditional ‘windbox’
(Jeng xiang ), double-acting piston bellows). The furnace could operate continuously
for 6-7 days before it was necessary to repair the inner lining and replace
the taphole stones. During this period charcoal and ironsand were charged, and
molten iron tapped, several times per hour. Reports from different times and
different places in the region indicate that daily production of pig iron was between
0.6 and I.2 tonnes, and that the amount of charcoal needed to produce one tonne of
pig iron was between 2 and 7-5 tonnes. Labour at the furnace was on the order of
10 worker-days per tonne of iron produced.//
Для слива чугуна наклояется вся печь.
Получением магния
//По способу Девилля расплавляют безводный хлористый М., к которому для легкоплавкости прибавляют поваренной соли и плавикового шпата, в закрытом тигле, затем бросают потребное количество мелко нарезанного натрия; М. выделяется в виде порошка и всегда содержит азотистый М. (см. ниже); продукт плавят и перегоняют при белом калении в закрытом тигле, через дно которого проходит пароотводная трубка (как при перегонке цинка). По этому способу работают заводы в Бостоне, в Манчестере.//
Для модифицирования чугуна перегонять магний от нитрида, конечно, не нужно.