Кричное железо и сталь (сначала сырцовые, а затем передельные и пудлинговые) использовались для изготовления инструментов и оружия на протяжении тысячелетий. При грамотной обработке, состоящей в первую очередь в многократной проковке для гомогенизации и выжимания остатков шлака, удавалось получить весьма качественный материал. Но настоящую однородную сталь можно получить только переплавкой — например, в тиглях.
История тигельной стали началась достаточно давно. По всей видимости, впервые выплавлять высокоуглеродистую сталь начали на юге Индийского полуострова в VI-V вв. до н.э. В дальнейшем подобные технологии достаточно широко использовались на Шри-Ланке, на Ближнем Востоке и в Центральной Азии, а также в Китае. Сталь получалась различными способами — науглероживанием кричного железа, сплавлением железа с чугуном или восстановлением железной руды (или скорей частично восстановленного агломерата из сыродутного горна) в тигле. Тигли, способные выдерживать высокие температуры и достаточно устойчивые в образующимся шлакам, были ключевым элементом технологии, и зачастую глину для тиглей импортировали.
Для достижения температуры плавления железа использовался специальный тип печи в виде купола, внутреннее пространство которого заполняли тиглями и топливом, обычно древесным углем, воздух же для горения обеспечивался интенсивным дутьем.

Древесный уголь — не очень подходящее топливо для плавления железа, так как очень быстро прогорает, а высокая пористость делает очень сложным достижение высокой температуре — уголь активно реагирует с углекислым газом с поглощением тепла:
C + CO2 = 2CO
Поэтому древняя тигельная сталь получалась только высокоуглеродистой, а за счет недостаточно высокой температуры — обычно неоднородной, что в итоге привело к легендарному булату.
В Европе производство тигельной стали было впервые организованно в 1740 г. Бенджамином Хантсманом, который в поисках лучшего материала для часовых пружин разработал способ переплавки цементной стали в тиглях. Способ Хантсмана на протяжении почти 150 лет использовался практически без изменений — увеличивалось лишь количество переплавляемого за одну загрузку металла и менялся состав шихты — и был основным способом получения качественной инструмениальной или оружейной стали.
Плавка стали производилась в самодувных горнах, приток воздуха в которые обеспечивался тягой дымовой трубы. Горны, или плавильные ямы, рассчитанеые на 1, 2 или 4 тигля, обычно располагались в ряд вдоль стены с дымоходами.

Сами тигли, которые требовались в больших количествах, готовились из огнеупорной глины, с добавлением шамота или графита в самой сталелитейной мастерской и сушились несколько недель на стеллажах над плавильными ямами.
Высушенный тигель обжигали прямо в горне, и затем загружали металл — цементную сталь или смесь железа с чугуном или древесным углем, также добавляли верхушки ранее отлитых болванок и флюс — обычно зеленое бутылочное стекло. Вместимость тигля при этом составляла 15-30 кг металла. Сверху плотно примазывалась крышка, а сам тигель устанавливался на колосники через прокладку из огнеупорной глины, предотвращаюшей дно от охлаждения воздухом. В качестве топлива практически всегда использовался кокс, расход которого составлял двух- трехкратное количество от выплавляемой стали, древесным же углем пользовались редко, так как его расход был в несколько раз выше и нужная температура достигалась с трудом.
Сама плавка длилась 2-4 часа, после чего тигель доставали из ямы и расплавленный металл выливали в изложницу.
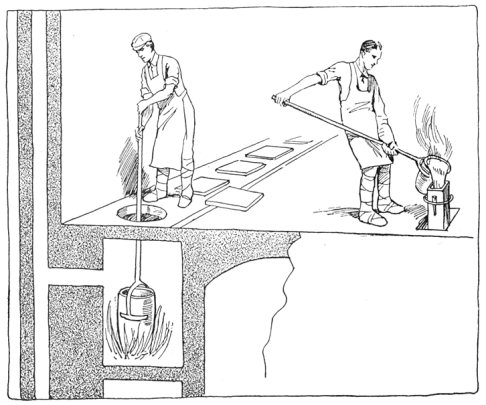
Ключевым фактором, обеспечивающим высокое качество получающейся стали, было время выдержки после плавления — недодержанная сталь получалась неоднородной, а передержанная — с большим количеством пузырей из-за растворившихся в жидком металле газов. Сама операция отливки тоже требовала большого мастерства и силы — металл из 30-кг тигля нужно было вылить непрерывной струей, не касающейся стенок изложницы, и не допустить попадания шлака.
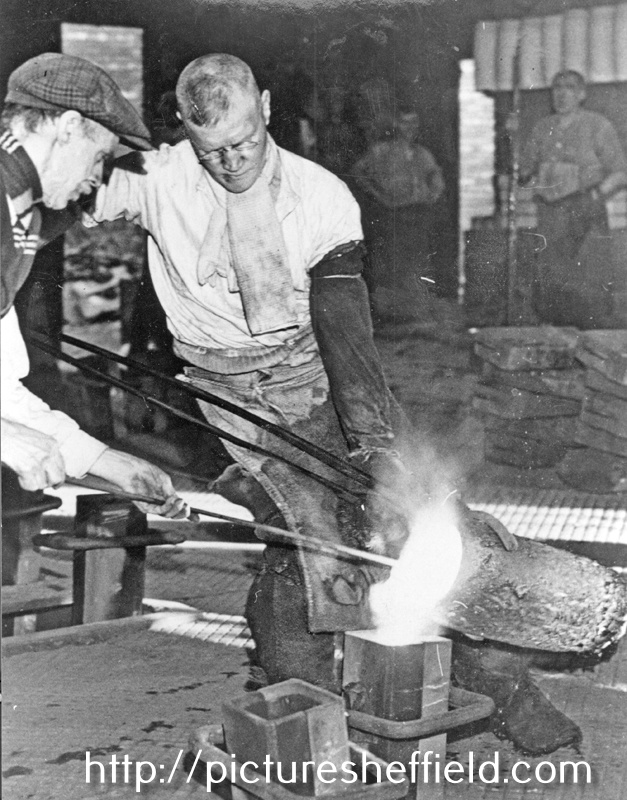
На русских заводах изложницы обычно смазывали бараньим салом, которое обеспечивало восстановительную среду и препятствовало образованию пузырей. После остывания верхнюю часть слитка с усадочной раковиной отрезали и добавляли в следующую плавку, а сам слиток проковывали и использовали для изготовления слесарных и столярных инструментов, бритв, столовых приборов, оружейных стволов и т.д.
Таким же способом отливали не только отдельные слитки, но даже и загототовки пушек, весом в многие тонны, собирая металл из сотен тиглей. Сталь для крупных отливок часто плавили ускоренным способом, помещая в разогретые тигли железо, магнитный железняк и заливая чугуном, предварительно расплавленным в вагранке — так отливали пушки на Обуховском заводе.
По сравнению с конвертерной или мартеновской сталью тигельная сталь была сильно дороже, но тем не менее производительность типичной мастерской в Шеффилде с 12 горнами и семью рабочими составляла около 25 тонн стали в неделю (6 рабочих дней с тремя плавками в день), а производство всех шеффилдских заводов в конце XIX в. — более 1000 тонн только лучшего сорта инструментальной стали в неделю (не считая стали низших сортов и мягкого литого железа для котельных листов и заклепок). В больших объемах тигельная сталь производилась также в Германии, России, США и других странах.
Кроме обычной углеродистой стали в тиглях плавили и легированеые — например, вольфрамовую сталь. Тигельная сталь постепенно вытеснилась сталью, выплавляемой в электропечах, однако последние заводы были закрыты в 1950-х — почти 200 лет с начала производства стали Хантсманом.
Лимитирующие факторы для более раннего внедрения тигельной стали — высокотемпературные огнеупоры и кокс (хотя в России использовали и древесный уголь). Также стоит дополнить технологию плавки введением раскислителей (кремния, марганца, магения, алюминия и др.), которые предотвращают образование пузырей в отливке. Тигельный горн отлично подойдет для выплавки легированных сталей — быстрорежущей (1% углерода и 5-20% вольфрама или молибдена) или марганцевой стали Гадфилда (1% углерода и около 13% марганца).
/По всей видимости, впервые выплавлять высокоуглеродистую сталь начали на юге Индийского полуострова в VI-V вв. до н.э. /
это знаменитый вутц?
В общем, да
Насколько я знаю, один из главных секретов тут — хороший материал самого тигля, чтобы выдерживал много плавок.
Набор цитат из загашников:
// Бессемер не без юмора вспоминал, как на его пред-
ложение — заменить железные рельсы стальными —
главный инженер, мистер Рамсботтом (John Ramsbottom)
посмотрел на него с удивлением и ответил: «Мистер Бес-
семер, Вы, должно быть, хотите, чтобы меня отдали под
суд за смертоубийство».
// Но Рамсботтом недаром считался одним из лучших
инженеров Англии – он живо схватывал технические но-
винки. Бессемеру удалось убедить его, что предлагаемый
стальной рельс имеет мало общего с твёрдой, но хрупкой
тигельной сталью. «Пришлите мне, пожалуйста, тонн де-
сять этого материала, чтобы я мог его вволю потерзать»,
– попросил Рамсботтом. И действительно, Рамсботтом,
получив пробные рельсы, на совесть занялся их «терза-
нием». Рельс в холодном состоянии был закручен што-
пором и лопнул только после того, как наружные сто-
роны вытянулись больше чем в полтора раза против
первоначальной длины. Затем стальной квадратный брус
(сечением 10?10 см) в горячем состоянии закручивали
вдоль продольной оси до тех пор, пока он не лопнул.
// К концу 1860-х годов общество Шеффилдского завода
было ликвидировано, а его пайщики получили долю, ко-
торая в 24 раза превышала первоначальный вклад. Диви-
денды в 57 раз превосходили сумму основного капитала.
К моменту прекращения действия патентов Бессемер по-
лучил по ним около миллиона фунтов стерлингов.
// По способу Хантсмена цементированную сталь переплавляли под слоем флюса из
зелёного стекла в огнеупорном тигле, установленном в печи с естественной тягой и от-
апливаемой коксом. Для переплавки отбирали полосы шведской цементированной
стали с такой твердостью, какую хотели получить в готовом виде. Эти полосы рубили
на мелкие куски, загружали в большой глиняный тигель, вмещавший 34 фунта металла,
и ставили его в печь. Печь, сконструированная Хантсменом для плавки в одном тигле,
имела площадь пода 114,3 см2 и высоту 76,2 см. В тигле переплавляли до 4,5 кг цементи-
рованной стали. В ходе плавки рабочие изредка поднимали крышку тигля и следили за
состоянием расплавленного металла. Готовность стали определяли «на глазок»: металл
должен был «блестеть, как солнце в совершенно ясный день, когда на него смотришь
невооруженным глазом».
Готовый тигель вынимали из горна, снимали крышку, удаляли небольшое количество
собравшегося наверху шлака. Сталь выливали в чугунные формы разных размеров. При
разливке металл получался губчатым и нуждался в проковке тяжелым молотом. Ти-
гельная сталь была чище и однороднее по составу, чем обычная цементированная. Она
оказалась замечательным материалом для изготовления ножей, бритвенных лезвий,
часовых пружин и маятников.
// Громоздкость тигельного производства лучше всего иллюстрируется на примере отливки крупных 20 — 40 — т слитков, которые в свое время производились из тигельной стали на заводах Круппа. Для выполнения этой задачи требуется к строго установленному сроку подготовить 15 — З0 тигельных печей с одинаковым составом стали в 900 — 1 800 тиглях; от 450 до 900 сдвоенных тиглей непрерывной вереницей в определенной строго установленной последовательности должны подаваться вручную к месту разливки с таким расчетом, чтобы струя стали не прерывалась ни на одну секунду; на производство такой операции одновременно на короткий срок задалживалось по два рабочих на каждый сдвоенный тигель только для подноски его или всего 1 000 — 2 000 чел.
// Тигельный булат, по-видимому, впервые был изготовлен ещё в VI в. до н. э. в Южной Индии, однако получил минимальное экспортное распространение лишь с V в. до н. э., а о масштабном производстве можно говорить лишь со II в. до н. э. Основной особенностью «вутца» была крайняя дороговизна, связанная с необходимостью использовать очень качественные руды и смешивать их с графитом в тигле, где выплавка превращалась практически в рулетку. Вместе с тем, получавшийся продукт был близок современнным сталям по качеству и содержанию углерода, что делало его очень привлекательным для оружейников. В результате возникли новые литейные производства на Шри-Ланке, мечи из готовых слитков делали в Китае, в Дамаске (оттуда «дамасская сталь») и в Иране, где впоследствии появится собственная технология стали, известная как булат (но о ней ниже). В Индии же попытки наладить массовое производство рафинированных сталей привели к изобретению штукофенной печи, сильно повысившей выход готового продукта. В I в. н. э. штукофенные печи появляются в Китае, однако их распространение будет сильно ограничено до раннего Средневековья.
// До середины XIXв., пока сталь была сварной, цементованно-кричной, т.е. пористой – ковка уплотняла её, выдавливала шлаки и делала сталь лучше. Как только появилась литая сталь, было замечено, что ковка её ухудшает. В металле накапливались зоны напряжений, микротрещины, шёл рост зерна, выгорание углерода, насыщение серой и кислородом. Никакого пресловутого уплотнения в чистом литом металле не происходит, об этом уже было сказано. Для того, чтобы это заметить, надо смотреть на результат. Если у вас на пол упал клинок и рассыпался – ведь это результат вашей ковки и термообработки, поскольку изначально была взята хорошая сталь. Условия реальной ковки весьма далеки от идеальной. Вместо газа и древесного угля топливом служит кокс и каменный уголь – идёт насыщение серой. Нагрев ведётся в окислительном пламени – выгорает углерод. Первый нагрев чересчур быстрый – возникают трещины. Часты перегревы – растёт зерно. Нет отжига перед закалкой – остаются зоны напряжений, и металл ломается сразу, или через время. Всё это в сумме ведёт к многократному ухудшению свойств металла. Не один -два удара разрушают сталь, а долгий путь, на котором ошибки только накапливаются, но не компенсируются.
Я принёс вам плохую новость, ребята, но убивать меня не надо – этой новости ровно 140 лет, поскольку как раз столько лет назад Д.К.Чернов исследовал сталь и доказал, что литые, штампованные или прессованные детали – прочнее, чем кованые. Именно с тех пор наука рассматривает ковку, как разрушение металла и только по этой единственной причине кузнечное дело плавно сползло на обочину прогресса. Тем, кому не достаточно авторитета Д.К.Чернова привожу слова известного кузнеца Пампухи И.Ю. : » Чрезмерное ковка тоже лишнее, всё можно разрушить. Ковать можно по разному, можно перегревать металл, можно не догревать и при закалке будет крошиться» «Пять охот» №4 Апрель 2007года. Кузнечный молот на заводе стоит там, где без него не обойтись и выполняет одну –две операции: прошивка, перемешивание. Сейчас даже смешно представить, что коленвал автомобиля будут ковать – он будет во много раз менее прочным, чем литой. Штамповочный пресс наносит гораздо меньше вреда, чем молот, поскольку деталь испытывает равномерное давление во всём объёме и не остаются зоны напряжений. Очень прочные сабли делались так: нагретый, слегка согнутый круглый пруток из стали У-7А попадал в валки, поперёк них, и на выходе падал в закалочную ванну. Высокое качество и повторяемость результата, брак мог быть только из-за дефекта металла. Просто мысленно сравните с длинным путём ковки этой сабли и сложностью её закалки – брака будет не 1%, а 30% — 60%.
// Булат – самая плотная из всех видов сталей, сжимать его – всё равно, что воду уплотнять. Поэтому предложение осаживать его – это призыв к его разрушению. Древние мастера знали, что ковка портит литую сталь. В то время был один вид литой – тигельная (булат, как частный её случай).Можно вспомнить кузнецов Гань Цзяна и его жену Мо Се (трактат «Хуайнань Цзы»), которые лучшие свои мечи отливали (хотя китайцы нам не указ). Многие карды, пустотелые булавы и мечи отлиты из булата (но, возможно, они просто показывали уровень своего мастерства в литье).
Егор Самсонов был слесарем – термистом, но никак не кузнецом, поскольку не выковывал свои ножи, а вытачивал из рессор (делал он так, конечно же, из-за лени и переизбытка сырья). Можно вспомнить и меня, как самого древнего из живущих кузнецов, который ещё в прошлом веке написал, что «плохая сталь под молотом уплотняется, а хорошая – разрушается» (статья «Просто кованый»), причём заметил это сам, ещё не читая Д.К.Чернова. Всё это шутки, в которых доля шутки, но вот доказательство, которое не отметёшь: разрубание вутца по спирали. Минимум ковки, минимум деформации и разрушения. Есть объяснение, что делалось это ради рисунка – попытка переноса современной психологии в средневековье. Это сейчас всё делается ради рисунка, а в те времена, когда от качества оружия зависела жизнь – боролись за качество. Достигнутому качеству соответствовал определённый рисунок, повторить его можно было, только повторив весь процесс и вновь достигнув такого же качества.
// Холодноковкость.
Это свойство определяющее. Закаленный булатный клинок можно положить на наковальню и ковать в холодном виде – он не треснет. Булат закален очень слабо: или на воздухе, или в кипящем жире, т.е. примерно так, как коса. Булатный клинок можно согнуть на 90 ?и выпрямить в холодном виде.
Булат-дамаск не обладает большой твердостью – это следует из его неоднородной структуры. Ведь в структуре булата нити, кристаллы, чешуйки мягкого железа перемешаны с кристаллами цементита и дендритами высокоуглеродистой стали. Если замерить твердость такой смеси, то алмазное острие измерительного прибора на разных участках будет показывать разную твердость, но в основном не высокую, т.к. размеры частиц соизмеримы с диаметром закругления острия алмаза измеряющего прибора и это острие будет соскальзывать с твердого кристалла на мягкий. По этому поводу П.П. Аносов и сказал, что «твердость относительна». «Дамасская сталь обладала достаточной твердостью, чтобы держать остроту» [4]. Если Вам предлагают булат твердостью 80 ед. HRC, то это инструментальная сталь с напылением карбида вольфрама.
Тигли в любом случае служили 1-4 плавки, только в газовой печи Сименса удавалось делать до 10 плавок.
//Как только появилась литая сталь, было замечено, что ковка её ухудшает//
Это абсолютно неверно. Ковка или прокатка необходимы после отливки, ухудшить может лишь грубое нарушение технологии. Ранняя литая сталь вообще содержала много газовых пузырей, но и без них ковка нужна для измельчения кристаллов, работы Чернова как раз этому и посвящены. В начале XX в. без ковки отливали лишь некоторые детали типа валков, колес, рельсовых крестовин и т.д. Высокоточное литье из стали появилось лет 50-70 назад, и свойства полученного металла все равно хуже, чем после ковки, прокатки или объемной штамповки.
Китайцы мечи (не лучшие, а худшие) действительно отливали, но не из стали, а из чугуна, и потом выжигали избыток углерода.
Состоится ли битва на виртуальных мечах — кованом и литом?
проверяли не раз — кованный лучше.
Ну литые из стали без ковки/прокатки и не существовали никогда
Мечи? Бронза например
Так сталь же обсуждаем, при чем тут бронза? Вообще чисто литые из углеродистых сталей изделия не очень часто встречаются, особенно в быту. Разве что китайские инструменты типа пассатижей, ключей и молотков — но они ломаются очень легко.
Да и бронза без горячей/холодной ковки для мечей не годится.
Я слыщал что у Ругеров ствольные коробки литые. А еще есть литая танковая броня…
Ну и обычного пистолета Макарова рамка, курок, спусковой крючок — высокоточное литье. Но это компромис доя удешевления производства, свойства металла там заведомо хуже, чем у отфрезерованных из поковки или проката деталей.
Иногда литье действительно лучше, но обычной углеродистой или среднелегированной стали это не относится.
Не надо сводить все к крайностям. В цитату вполне себе говорится о механической обработке.
// Чрезмерное ковка тоже лишнее, всё можно разрушить
// круглый пруток из стали У-7А попадал в валки
Я лично воспринимаю эту цитату как констатацию факта — если долго ковать, то никакого чудо результата не будет.
Насчет ковки — для каждого конкретного случая (марка стали, назначение изделия, его форма и т.д.) есть оптимальная степень уковки (укованности), она может быть от 1.5 и до 20 в отдельных случаях.
https://mash-xxl.info/page/239231008147160064160014166106144121103180080138/
Понятно, что бездумная ковка, да еще с нарушением технологии, может испортить лучшую сталь. Особенно в случае булатоподобных материалов, имеющих очень узкий диапазон температур ковки.
кованный, может быть, и лучше, а вот кованый — не знаю
Опечатка ? — ведением раскислителей (кремния, марганца, , алюминия и др.)
Далеее по тексту — Пампуха весьма уважаемый кузнец как в нашей среде, так и мной лично, но Игорь Юрьевич все же не последняя инстанция.
Чернов — так же не идол. Спорить я не буду, это долго и мнения не истребимы))
ИМХО, ковка мвстера способна из простого железа (Ст3 например) сделать шедевр, сравнивый с порошками по свойствам на ноже и превзойти их на длинном.
Ковка халявщиком только увеличит число дефектов.
Резюмируя, без хороших ствлей только мастерство кузнеца позволяет делать качественные вещи. Имея под боком металлобазу с полным марочником сталей — люлой сможет выточить хороший нож/меч
Алюминий — раскислитель для стали, особенно для фасонных отлмвок, никакой опечатки нет.
Ст.3 находится на границе прокаливаемости, и без дополнительных приемов типа цементации твердости у нее не будет никакой.
Ошибка копирования — там слово МАГЕНИЯ — (кремния, марганца, магения, алюминия и др.)
По Ст3 — сам пробовал в восстановительной среде ковать — нормальный итог можно получить
Да, и магний тоже годится, хоть и имеет низкую температуру кипения
Что такое нормальный итог? 20-25 hrc — это все, что можно из ст.3 получить без поверхностной ХТО.
В восстановительной атмосфере горна или с восстановительным флюсом происходит науглероживание поверхности. Это старый метод, применялся до прошлого века (может и сейчас). Причем если долго «углеродить» — там слой до мм дойдет, а это уже МНОГО
http://popadancev.net.s3-website-us-east-1.amazonaws.com/cementaciya-zheleza/
Я сам цементировал детали спускового механизма пневматической винтовки, процесс это небыстрый. Опять же, для ножика сгодится, а для меча вряд ли, слишком мягкая сердцевина не даст достаточной жесткости. Тут не ст3, а ст45 надо хотя бы брать, она уже калится.
Самое интересное начинается при переходе от однородных материалов к композитам (те же упомянутые дендриты одной стали в матрице другой, и т.п.). Тут нынешнее материаловедение недоразвито, даже банальную анизоторопию при прокате/штамповке/ковке рассчитать проблематично…
Так что «ще не сгинело» материаловедение сталей как наука, есть куды развиваться.
А кустари (куда всех «чудо-кузнецов» отнесём) — максимум, на случайный, под конкретную задачку, рецепт натыкаются… до первого изменения в сырье. Неформализуемо, неповторяемо, и попаданцу бесполезно :).
/Неформализуемо, неповторяемо/
и поэтому науке тут делать нечего
+1
Подозреваю это и есть основной источник БЕСКОНЕЧНОСТИ кузнечных ср;чей. Обсуждается тема которая до сих изучена не до конца.
Не знаю, по-моему все «секретные технологии древних», которые имеют реальную основу, а не сказку, вполне изучены и при желании воспроизводятся.
касательно композитных материалов может быть N+1 фаз, каждая из которых образуется в уникальных условиях. Если нет детального описания, повторить практически невозможно. Кроме того, ранее не было измерительных приборов, как понять — получилось или нет? Меч, которым можно подпоясаться и которым же можно разрубать гвозди, и на котором падающий шелковый платок разрезается пополам под действием собственного веса — правда или вымысел?
//Меч, которым можно подпоясаться и которым же можно разрубать гвозди, и на котором падающий шелковый платок разрезается пополам под действием собственного веса//
Как в анекдоте: быстро, дешево, качественно — выбирайте 2 из 3
Я не о секретных технологиях, а о понимании. Даже лезвия в стандартизованных современных условиях это большая и сложная наука, в которой до сих пор идут исследования.
А те условия что существовали в средневековой кузне и вовсе не изучались.
И вот пытаемся понять почему у кузнеца такого-то вдруг начало получаться, и получалось у его сына и внука, а у правнука перестало. Они не понимали почему — они повторяли заученный набор действий, включая заговоры и ритуалы. Мы не понимаем почему — сложная это штука.
Но объяснение найти хочется и начинается лабуда про миллиарды слоев металла, кобальтовые примеси в руде, охлаждение клинка в теле раба и тп тд
//А те условия что существовали в средневековой кузне и вовсе не изучались//
С этим сложно согласиться, за 50-70 лет археометаллургия развилась очень сильно.
Ну про вовсе не изучались это я конечно перегнул.
Но скажем когда я поискал детали о китайской металлургии — нашел какие-то крохи. Имхо зияющих дыр полно.
детали — в смысле конкретные анализы металла по разным периодам, с твердостью, структурой и тп тд
А может просто это никому нахер не надо?
Все эти истории про чудомечи рассказывают в лучшем случае торговцы-шарлатаны а чаще всего-фрики. На самом деле не важно как делается лучший меч. Важно как наштамповать мечей на всю армию. А то что они будут уступать в качестве работе мало-мальски умелого кузнеца-на поле боя не важно.
Вот тут, например
http://donwagner.dk/index.html
Основной нерешенный вопрос по Китаю — была ли там древная сыродутная металлургия, или от бронзы они сразу к чугуну пришли
https://www.google.com/url?q=https://insa.nic.in/writereaddata/UpLoadedFiles/IJHS/Vol44_3_2_WLox.pdf&sa=U&ved=2ahUKEwitkNbPuJDuAhWn4YUKHXMUAWgQFjAAegQIBhAB&usg=AOvVaw2AYRiySkeqYT8n5F0F9n_2
Катайская тигельная сталь
// http://donwagner.dk/index.html
Этот сайт я знаю, ссылался уже, тут например http://popadancev.net.s3-website-us-east-1.amazonaws.com/backward_europe/#comment-148989
// BINTIE: THE WOOTZ STEEL IN ANCIENT CHINA by WILLIAM LOX
Хороший пример. Два упоминания состава в Table 1 и Table 2, источники не гуглятся, непонятно к какому году относятся данные и какая выборка. Про твердость/структуру вообще ничего.
Даже по русской металлургии находится на порядок больше, а уж по европейскую и говорить нечего.
—
Я конечно жалкий любитель, возможно есть куча материала исключительно на китайском. Но по прошлому опыту сомневаюсь. Искал скажем данные по остаткам кораблекрушений — у китайцев на первый взгляд околонулевые цифры. При более подробном изучении находятся упоминания о десятках, но для европы находятся базы данных на пару тысяч.
>у китайцев на первый взгляд околонулевые цифры. При более подробном изучении находятся упоминания о десятках, но для европы находятся базы данных на пару тысяч
Китайцы врали в статистике еще до ее изобретения.
Хотел спросить, а при какую максимальную температуру можно получить при сжигании кокса? Просто когда вижу описания таких печей, все время хочется добавить регенератор. Температура возрастает, расход топлива уменьшается…
Собственно введение предварительного подогрева и стало одним из важнейших прорывов в металлургии. Доиндустриальную металлургию часто называют сыродутной — это просто обозначение печи без подогрева воздуха.
// хочется добавить регенератор
в современных и юзается, обсуждали хотя бы в http://popadancev.net.s3-website-us-east-1.amazonaws.com/regenerativnaya-pech/
Поскольку в тигельном горне плавили не только углеродистую сталь, но и мягкое железо, температура в тигле должна была быть не менее 1600-1650. В принципе, можно пытаться ферросилиций выплавлять, или карбид кальция.
Рекуператор для подогрева воздуха, конечно, был бы очень полезен, например такой
https://mash-xxl.info/page/128188211044057130010214138077199163011074031044/
Это усложнит конструкцию, придется добавлять принудительную подачу воздуха.
Не вижу проблем с рекуператором и без принудительной подачи… достаточно длинная труба (можно по склону) — вполне заменит наддув.
По собственно устройству — что периодическая схема (Мартен, ага), что противоточная, что просто нагрев второй печкой на некондиционном топливе… разница не принципиальна.
Усложнение останется, но сугубо в смысле низкоквалифицированной возни с глиной/кирпичом/etc.
Низкоквалифицированной возни с жаропрочным кирпичом.
Кстати как его вообще делали? И как часто надо было менять?
Для простого рекуператора ничего особо жаропрочного не надо. На уровне бытовой печной трубы или любой керамики.
Вообще нет. Для регенератора периодического действия важна высокая теплоемкость, теплопроводность и стойкость к термоциклированию. Жаростойкость — тоже, выходящие из печи газы никак не меньше 1200. Поэтому нужен плотный шамотный кирпич.
Для противоточноного — и жаростойкость, и теплопроводность.
Для выплавки стали в требуемых попаданцу количествах хватит и простого горна.
Это если делать оптимизированный на современном уровне, то «нет».
А «вообще» — «да».
Подогреть воздух до 500-600С, к примеру, можно в чём угодно.
Да насыпать хоть крупного щебня, и гонять через него, пока в песок не развалится и сопротивление не вырастет в потолок.
Чтобы подогреть воздух до 600, насадку рекуператора нужно раскалить гораздо сильнее (в том же мартене насадка нагревается газами с температурой под 2000, а воздух от насадки — о 1000-1200). Учитывая маленькую теплоемкость щебня и непредсказуемое движение в нем газовых потоков, переключать рекуператоры прийдется слишком часто (это организовать тоже не так просто). В общем, эффект скорей всего будет недостаточный, чтобы все это городить.
Противоточный теплообменник или отдельная печка попроще будут, но тоже не принципиальны — даже 5-6 тонн угля на тонну стали вполне терпимы, а поскольку из горна выходит по сути генераторный газ с температурой за 1000 градусов (а ближе к 1300-1400), который можно утилизировать для менее требовательных процессов (плавка чугуна или меди, прямое восстановление железа, обжиг керамики и т.д.), то суммарная энергоэффективность сильно вырастет. Подогревать воздух для повышения температуры выше достижимых в самодувном горне 1600+ имеет смысл только после качественного прорыва в огнеупорах хотя бы для тиглей.
По большие сложности для 500-600 всё же не соглашусь, всё решается масштабированием и т.п., но спорить лень — вопросы сугубо технические.
Противоточный теплообменник в чем-то проще, а в чём-то наоборот… вот ему теплопроводность более важна, т.е. железные комплектующие и/или относительно тонкая керамика.
Печка — да, менее требовательна — и вполне дополняет почти любой дохленький рекуператор.
Про тигли всё верно, там без огнеупоров не обойтись, в отличие от рекуператоров.
Но даже штукофен/блауофен дуть хоть немного горячим — большой прорыв может быть, хотя бы в возможности использования дерьмового топлива и свободы масштаба и дизайна, не привязанных к необходимости выжимать всё до последнего градуса из сыродутья.
Мы же вроде тигельный горн, а не блауофен обсуждаем, и тигельному горну в максимально простом варианте подогрев не нужен.
Домна — другое дело, но опять же есть свои нюансы. Например, если чугун нужен не для переплавки в железо, то излишняя температура тоже может быть вредна, так как сильно повышает содержание кремния. Часто это не нужно и даже вредно.
//необходимости выжимать всё до последнего градуса из сыродутья//
Это, кстати, достаточно распространенное заблуждение.
А по факту свежевыжженный древесный уголь оставляли вылежаться на воздухе, чтобы он набрал некоторое количество влаги. Иначе ход плавки получался слишком горячий — при плавке на крицу много чугуна получалось, а при доменной плавке — быстрый разгар горна.
>>Древесный уголь — не очень подходящее топливо для плавления железа, так как очень быстро прогорает, а высокая пористость делает очень сложным достижение высокой температуре — уголь активно реагирует с углекислым газом с поглощением тепла<<
А если делать брикеты из прессованной угольной пыли? Так можно гарантировать однородность и высокую плотность угольного брикета. И никакой пористости не будет!
Пористость, конечно, полностью не устранить, но хотя бы насыпную плотность древесного угля поднять можно. Медленней прогорать будет.
/А если делать брикеты из прессованной угольной пыли?/
https://otivent.com/briketirovanie-uglja
вот описана технология брикетирования «в домашних условиях» (после описания промышленной)
Попаданческого там мало
Да вроде простой ручной рычажный пресс — формователь. Можно хоть из дерева сделать, но желательно часть деталей все же металлические.
Сырье измельчить, смочить водой и добавить связующее (например крахмальный клейстер в количестве 1%, деготь, мазут, битум или еще что то жидкое и горючие, на худой конец глина), сформовать и слегка спрессовать, просушить. Все.
Можно при желании добавить углеводороды чтобы не повышать зольность.
По ссылке каменноугольные брикеты
не понял-а мы какие обсуждаем
Интересно, что для выплавки булата/вутца нужна значительно меньшая температура — всего 1400 градусов при содержании углерода 2-2.1%, или даже ниже, за счет высокого содержания фосфора.
Самая маленькая установка доя электрошлакового переплава
https://epos-nsk.ru/portfolio/ustanovki-ehshp-ehshl/#1599795895716-a17e1d5d-b7bb
Мощность 17 кватт, производительность до 10 кг в час. Вот только откуда 17 кватт взять?
http://donwagner.dk/tiny.html
Это, конечно, не тигельная сталь, но тоже интересный вариант. На пару напильников точно хватит.
Очень похожее описание процесса получения стали в De re Metallica Агриколы.
Не ожидал, что такая милипусечная хрень без внешнего подогрева и на сыродутье таки даст сталь.
Я бы её теплоизолировал, конечно — хоть древесным углём снаружи обложил… и дул хотя бы через глиняную трубку, проложенную через костёр, каждая сотня градусов — в копилку… но если и так сработало… только интересно, чем они дуют — пылесосом, что-ли? 🙂
Что тут радует — малый масштаб позволяет заниматься дешёвой оптимизацией.
У Агриколы яма фут в диаметре и фут глубиной. Там, очевидно, не просто плавление, а науглероживание части металла до чугуна, его плавление и перемешивание с остатками железа на дне горна.
Почти тигельная))
Ну а с поддувом сложно развернуться. Основная проблема — чем нагнетать воздух в те времена. Мехами большие объемы не осилить, а малые и так все тогда делали.
Оптималтная конструкция мехов — деревянные ящичные
https://www.hitachi-metals.co.jp/e/tatara/photo/p020611_2.gif
https://thecollector.b-cdn.net/wp-content/uploads/2020/11/chinese-inventions-blast-furnace-icon-768×545.jpg
По второй ссылке у меня «403 Forbidden»
Так — норм:
https://thecollector.b-cdn.net/wp-content/uploads/2020/11/chinese-inventions-blast-furnace-icon.jpg
не дается ссылка.
Но меха — это ручной труд, низкая производительность. В общем тяжко
Деревянная улитка — тоже вполне, на мой взгляд не хуже мехов.
Ну и если есть где тромпу поставить, и например цемент в наличии — вообще хорошо.
Да, так можно, но окупятся ли труды? Если только рабы — да и то недополученная прибыль от вероятной более эффективной деятельности
Сталь критична для ЛЮБОГО промышленного производства. Ну разве что тканцкий станок много стали не требует. Любые механизмы, нагруженые детали, элементы требующие высокой точности все это сталь. Чугун слишком хрупкий, железо слишком мягкое.
Если попаданец хочет прогресс то ему нужна сталь. Вопрос в том как получить ее много и стабильного качества. Ультимативное рещение-мартен но тут очень сильно встаёт вопрос с жаропрочным кирпичом да и мартен конструкция не маленькая. Вот и ищем альтернативы.
это я про брикетирование угля писал. Про необходимость стали у меня сомнений нет
А можно спдавлять чугун с окалиной для получения стали?
Можно, только чугун должен быть чистый. Похожим образом выплавлялась сталь по методу Ухациуса, сплавлениеи чугуна с железной рудой
https://www.sciencedirect.com/science/article/abs/pii/0016003257903848
https://journals.sagepub.com/doi/pdf/10.1243/PIME_PROC_1858_009_019_02
тигель для плавки золота из картошки https://www.youtube.com/watch?v=zbRzi90v4V0
Ну не надо троллить людей! Плавка на куске угля (а из картошки сделали уголь)- это ювелирная классика!))
А вот тигли для плавки сталей (булата например) — это уже проблема.
Про винтовки Бердана
//Важно отметить, что сталь, идущая на производство стволов винтовок, привозилась из Англии (завод Firth and Brother в Шеффилде) и Германии (завод Бергера в Вестфалии). Металлургия Соединенных Штатов не могла дать такой качественный металл. Причем прокованные болванки завода Бергера по качеству превосходили английскую продукцию.//
Отличная книга по истории металлургии — A history of metallurgy by Tylecote, R. F Немного старовата — 1976, дорого дал бы за что-то сравнимого качества, но этого века.
Относительно популярно, но с кучей таблиц и ссылок и иллюстраций. Скажем расход топлива на цементацию встретил в первый раз
// CEMENTATION STEEL
// the conversion of wrought iron to steel took place in a furnace containing three chests, 2 m long, which were heated for 6-7 days. It needed 100 t of charcoal to convert 450 kg of iron to steel. 11I3n order to try and reduce the cost of this mate- rial, some coal was imported from England.
// The result was not very homogeneous, with 1%C at the surface and very little at the centre and, after forging, the steel had a banded structure, often with residual slag along the welds be- tween the piled layers. No doubt this was why in 1740 Huntsman, the c1ockmaker, objected to it and preferred his more homogeneous crucible steel.
Интересные моменты вроде обжаривания руды и конструкции наконечников для подачи воздуха с водяным охлаждением после введения hot blast
// the puddling process was difficult to control in such a way as to leave a residual carbon content of the same order as that normally associated with steel, i.e. 0.5-1.2%.
пара иллюстраций
https://www.dropbox.com/s/4hjffh89vsvt1ne/A%20history%20of%20metallurgy%20by%20Tylecote%2C%20R.%20F%20p68.png
https://www.dropbox.com/s/gr3dz9bw2kkn6t0/A%20history%20of%20metallurgy%20by%20Tylecote%2C%20R.%20F%20p183.png
Это отличная книга.
Если случайно найдете, где можно скачать R. F. Tylecote. The early history of metallurgy in Europe, 1987, киньте, пожалуйста ссылку.
Насчет 100 тонн древесного угля на 450 кг цементной стали — это, вероятно, ошибка. Древесный уголь жгли только в России и Швеции
//The only other process consumable was the fuel used for heating the furnace. This varied according to location and availability but as far as this country was concerned it was invariably pit coal; indeed, the location of the industry seems to have been determined by the two factors of availability of coal and access-ibility of supplies of Swedish iron. Abroad, the situation was sometimes different. Certainly in Sweden the furnaces were wood or charcoal fired, whilst in Germany and Austria there is evidence of the use of lignite.//
И расход не такой катастрофический
//A Newcastle furnace, on the other hand, had chests of 68 cubic feet capacity with a charge of 14000 lb//
//At Newcastle the firing lasts for five days and nights, during which time the consumption of coal amounts to four Newcastle cauldrons (or 84 Swedish barrels}*//
То есть около 13 кубометров каменного угля на 5-6 тонн стали. Много, но не запредельно.
В деталях процесс цементации и тигельной плавки описан в THE DEVELOPMENT OF THE EARLY STEELMAKING PROCESSES-AN ESSAY IN THE HISTORY OF TECHNOLOGY Kenneth Charles Barraclough 1981 .
Скорей всего имелось в виду, что на 450 кг железа загружалось 100 КГ древесного угля как карбюризатора, а не топлива.
Читал по диагонали, ошибся. 4 ньюкастлских калдрона, т.е. 10.6 тонн каменного угля, требовалось на цементацию 11 тонн железа.
Показалось подозрительно много, но какой соблазн просто объяснить закат технологии. (
Ну хотя бы https://www.dropbox.com/s/4hjffh89vsvt1ne/A%20history%20of%20metallurgy%20by%20Tylecote%2C%20R.%20F%20p68.png интересен — а то иные товарищи любят говорить что вот сначала пластины варили так, потом так. А выясняется что все способы были знакомы, видно в разных местностях использование варьировалось в зависимости от сырья/моды.
// Tylecote. The early history of metallurgy in Europe
Не, мои каналы ничего не дают. На амазоне вроде платная есть, я бы вложил тысячи полторы, но с тамошними ценами это куча народа нужна.
//Опыт показалъ, что наиболее удовлетворяют требованиям самые
чистые сорта глины, приближающиеся к составу А1203. 2 Si02. 2H20,
и встречаемые в третичной и меловой формацияхъ. В Германии залежи такой глины находятся: на Рейне — близ Валлендара и Мелема; в провинции Гессенъ-Нассау — в Гроссъ-Альмероде, близь Касселя, и в округе Мантабауръ. (Сельтерсъ); в Баварии близь Гркжштадта (Пфальцъ), въ Пассау и Деитендорфа; в Саксонии — близь Клингенберга: в Силезии — близ Заарау и др. В Богемии огнеупорная глина добывается близь Пильзена и Мельника; в Австрии — в Гёттвей и Леобене, в Штирии; въ Швеции — в Гёганесе, близь Гельзингборга. Из английских огнеупорных глин известны добываемыя в Стурбридже и Гарнкирке в Шотландии: из французских — — в Forges-les-Eaux; из бельгийских — глина,
добываемая в Гюи близь Намюра, в значительном количестве ввозимая в Германию. В России лучшими глинами для горшков считаются 1:
гжельская (Моск. губ.), пеньковская (Перм. губ.), андомская (Олонецк. губ.),
белевка (Тульск. губ.) и др. Киевская губ. по Днепру и Черниговская изобилуют хорошими глинами. В Новгородской губ. известна боровицкая глина, добываемая по берегам р. Мсты и Прикши и на земле г. Боровичей; из привозных глин иа русских заводах употребляетея голландекая белая глина, а в последнее время преимущественно богемская (меренская) или гессенская (Гроссъ-Альмероде). Иностранныя глины обходятся дороже, но доставляются в чистом виде и однообразнаго качества, тогда как наши
глинъи, будучи сами по себе превосходнаго качества, иногда доставляются
с значительным количеством (5% и более) колчедана, камней, травы и пр., а иногда даже с захваченным при выработке песком или мергелемъ, отмучивать который на заводе нет разсчета.//
//Experiments carried out to simulate the conditions in a
crucible furnace, with a twelve inch bed of incandescent
fuel, have shown that charcoal would give around 1425oC,
which would be insufficient for steelmelting, whilst coke
made from lumps of Barnsley hard coal would give l530oC —
barely sufficient. Beehive coke, however, gave a temperature
of 1600oC and it is stated that the latter fuel was 2 that used for the crucible process after about 1805.//
//The steel is not ready for casting until it has been in the
molten state for some considerable time or until,
as the expression used by the melters says, ‘it is killed’. Steel which has not been killed
teems ‘fiery’, that is to say it gives off a profusion of little sparks and appears to boil in the pot, while the ingot, when cold, will be full
of honeycombs. If the steel be too hot it will show the same fault, while if it be kept in the
fire too long it will be very rotten and brittle. Should a piece of coke fall into the crucible it will result in the steel being spoilt by the
sulphur present in the coke//
//When the charge is entirely molten, it is kept in
the furnace for one-half to an hour longer in order that it may teem ‘dead/ that is, pour quietly without the evolution of gas, and
yield solid ingots. If the ‘killing’ time is too long, the ingots will
be solid, but the steel will be hard, brittle and weak, probably as
a result of the absorption of too much silicon from the walls of the crucibles. Graphite crucibles probably yield more silicon than
clay crucibles. Just what takes place during the killing of steel
is not definitely known. Some have suggested that the gas contained in the steel is eliminated from it during this time, but the alternate suggestion that the principal effect of the killing is to cause the steel to absorb silicon, becoming sound on this account, is the more generally accepted one. The amount of silicon in the final steel will vary greatly, but will average perhaps from 0.10 to
0.50 per cent//
Долгую выдержку можно заменить добавкой раскислителя
//The rules for ‘killing’ or ‘deoxidation’ changed over
the years. The principle remained the same. Since silicon produced the desired effect, it was obvious that the addition of silicon metal or, more conveniently, of ferrosilicon (one of the so-called ‘ferroalloys’ produced as aids to the steelmaker and consisting in this case of an alloy of 45% or so of silicon, the reminder being
essentially metallic iron to the crucible, near the end of the melt, would obviate the need for the long ‘killing fire’ — when, of course, the role of silicon was understood.
Aluminium, however, was found to be even more effective than silicon and as little as one quarter to half an ounce of aluminium — often in the form of an
‘aluminium pill’ — would quieten most pots of crucible steel. The addition of aluminium to crucible steel was generally frowned on in the trade in Sheffield//
//Вылавка ферро-хрома изъ руды производится очень просто. Руду смешивають съ 12—15% древеснаго угля, 6—7 % колофониума, или истертой въ порошокъ смолы, около 5% битаго стекла и 10—12 % кварцеваго песку.
…
Масса поступаетъ затемъ въ графитовые или глиняные тигли, причемъ ихъ не наполняютъ до самыхъ краевъ, оставляя место для тонкаго слоя мелко-битаго стекла и более грубыхъ кусковъ древеснаго угля.
После этого тигель покрывается крышкой, которую плотно примазываютъ къ краямъ глиной, оставляя въ ней лишь небольшое отверстие
для выхода газовъ. Необходимой для возстановления окисловъ температуры можно достигнуть и въ самодувных печахъ съ хорошей тягой, но для получения хорошо сплавленной болванки въ настоящее время почти исключительно
применяются газовыя регеперативныя печи.
…
Выплавленный таким образомъ ферро-хромъ получается въ виде штыка
соответствующей внутреннему очертанию тигля формы и редко бываетъ
свободен отъ включений шлака и пустотъ. Въ изломе показывает серый
металлический блескъ. Сплавь этотъ применяется почти исключительно въ
качестве прибавки при производстве хромовой стали.
//
//Большой интерес учёных эпохи Революции в естествознании вызвал вольфрам. В металлическом состоянии он был получен братьями Элюар в Испании в 1783 г. Элюары провели широкие исследования по изучению сплавов вольфрама, которые они получали в тиглях «с угольной набойкой». //
//Усилия многих исследователей были подытожены английским инженером Окслендом, который в 1857 г. взял патент на получение железо-вольфрамовых сплавов. В тексте патента можно прочитать следующее: «Вольфрам, восстановленный из волчеца (вольфрамовой руды) углеродом, может быть смешан с рудой в доменной печи, или с чугуном в вагранке, в количестве до 30 %. Сплав чугуна и вольфрама может быть применён в металлургической технике… Хорошую литую сталь можно получить, прибавляя к ней от 0,5 до 25 % вольфрама. Сплавы железа с вольфрамом могут быть очищены и превращены в литую сталь обыкновенным способом цементования». Фактически мы видим описание полного технологического цикла получения и применения ферросплава, используемого для легирования стали.
Запатентованная Окслендом технология получения и применения «ферровольфрама» была реализована в промышленном масштабе в Австрии (её внедрение приписывается профессору Майеру из Леобена) в 1859 г. Спустя 5 лет вольфрамовую сталь производили несколько предприятий Австрии и Германии (её использовали для изготовления снарядов и холодного оружия). В 1864 г. Зиверт опубликовал состав стали, выплавляемой на сталелитейном заводе в Бохуме. Она содержала от 1 до 3 % вольфрама и около 1 % углерода.//
//Распространенным способом получения ферросплавов тугоплавких металлов, прежде всего феррохрома и ферровольфрама, в конце XIX– начале XX в. была плавка в вагранке – небольшой шахтной печи, схожей по конструкции с доменной.
…
Выплавка феррохрома и ферровольфрама в вагранках велась «на козла» – т.е. полученный сплав ввиду своей тугоплавкости не вытекал в жидком виде из печи, а оставался внутри неё в виде слитка – «козла». Вагранки устраивались с откидным дном для удобства извлечения слитка.
…
Плавку феррохрома вели на брикетах, состоящих из кокса, хромита, соды и смолы. Воздушное дутьё предварительно нагревали до 400-500 °С. Плавку вели до тех пор, пока «козёл» не затянет фурм для подачи воздуха, которые устраивались в три ряда по высоте вагранки (на фото представлена вагранка с одним рядом фурм).
За одну плавку получали около 3 т феррохрома. Длительность кампании, включая время на охлаждение и футеровку вагранки, составляло около 7 дней. Расход кокса достигал 5-6 т на тонну феррохрома.
Плавка ферровольфрама осуществлялась также «на козла», получали сплав с содержанием вольфрама 78-84 %. Содержание углерода обычно составляло 0,1-0,7 %, столько же марганца и кремния; доля меди, олова и серы – менее 0,1 % для каждого компонента.
Реакция восстановления вольфрама углеродом из минералов (вольфрамита, шеелита) при этом шла очень быстро, поскольку конечные продукты процесса энергично уходят из системы: образующийся СО – удаляется с отходящими газами, а частицы ферровольфрама, обладающие громадным удельным весом по сравнению со шлаком (удельные веса 16,0 и 3,0), легкоосаждаются на подину и, наплавляясь, образуют там «козёл». При этом верхний слой «козла» на подине вагранки представляет собой металлическое «болото», растворяющее вольфрам и железо. При нормально идущем процессе перегретые, подвижные частицы шлака, запутавшиеся в «козле», легко всплывают, и сплав получается монолитным. Поэтому после окончания плавки осуществляли выдержку для освобождения «козла» от включений.//
Резцами из закаленной углеродистой стали (например, тигельной) можно обрабатывать железные и стальные детали, но скорость резания при этом сильно ограничена — даже при интенсивном охлаждении происходит локальный перегрев до 200-300 градусов, при котором режущая кромка теряет твердость и тупится. Этого можно избежать, если использовать специальные стали, легированные вольфрамом или молибденом.
Даже небольшие добавки вольфрама сильно повышают прокаливаемость стали и обеспечивают мелкозернистую структуру, и с 1850-х годов вольфрамовую сталь начали применять для изготовления холодного оружия, стволов орудий и бронебойных снарядов. При увеличении содержания вольфрама способность закаливается повышается до такой степени, что нагретая и оставленная на спокойном воздухе сталь закаливается сама. Поэтому сталь, разработанная в 1868 г. Мюшетом и содержащая около 2% углерода, 2.5% марганца и 7% вольфрама, получила название самокала. Такая сталь оказалась более стойкой к перегреву, не теряя твердости при 300 градусах, и позволяла обрабатывать металл при скорости резания до 7 м/с, что в полтора раза превосходило максимально возможную для резцов из простых углеродистых сталей.
Однако настоящий прорыв произошел в 1899 г., когда Тейлор и Уайт обнаружили крайне необычные свойства стали, содержащей вольфрам и хром. При нагреве закаленной стали сначала происходило обычное падение твердости в результате отпуска, но при дальнейшем повышении температуры высокая твердость восстанавливалась, и сохранялась даже при температурах начала красного каления. Такое поведение объесняется тем, что при температуре около 500 градусов происходит выделение смешанных карбидов железа и легирующих элементов, так называемых вторичных карбидов, которые и обеспечивают повышение твердости.
Самые первые варианты быстрорежущих сталей, содержавшие 0.5-0.6% углерода, 3.5-4% хрома и 13-14% вольфрама, позволяли вести обоаботку со скоростью 25-30 м/с. Увеличение содержания вольфрама до 16-18% и добавление 1% ванадия позволило поднять скорость резания до 150 м/с, при этом сталь сохраняет высокую твердость, болен 60-62 HRC, до температуры 610-620 градусов. Этот сплав известен под маркой Т1 (в отечественном варианте Р18). Впоследствие было разработано множество других сплавов, в том числе м использованием менее дефицитного молибдена, а также дополнительно легированные кобальтом и имеющие еще большую красностойкость.
Кроме выплавки быстрорежущей стали необходимого состава не меньшее значение имеет последующая обработка. Слиток необходимо тщательно проковать для измельчения первичных карбидов и отжечь для последующей слесарной обработки. Закалка быстрорежущей стали сильно отличается от закалки обычной углеродистой, и простыми визуальными методами в этом случае не обойтись. Металл нужно нагревать очень равномерно до высокой температуры, около 1300 градусов, выдерживать некоторое время для максимально полного растворения карбидов, после чего закаливать в подогретом масле. Сразу после закалки производится высокий отпуск тремя циклами при температуре около 550 градусов, при этом остаточный аустенит распадается и получается структура, состоящая из высоколегированного мартенсита, устойчивого до 600-650 градусов, и вторичных карбидов.
Учитывая высокую стоимость быстрорежущей стали, из нее часто делают лишь небольшую часть инструмента, припаивая к державке из обычной углеродистой стали.
Если говорить о времени возможного внедрения, то наиболее привлекательным будет весь XIX в., когда все необходимые условия уже есть, а полезный эффект будет максимальным.
//Первым легирующим элементом, который стал применяться в промышленных масштабах, стал марганец. Соединения марганца, в первую очередь пиролюзит (МnО2), были известны и применялись с древних времён. В чистом виде марганец впервые получили в 1774 г. шведские химики Карл Вильгелм Шееле и Юхан Готлиб Ган. Название «марганец» (manganesium) приняла в 1787 г. Французская комиссия по номенклатуре, но всеобщим оно стал лишь в начале XIX в. Позднее этот металл, чтобы не было путаницы с открытым Хэмфри Дэви в 1808 г. магнием (magnasium), переименовали в manganium. В России в первой половине XIX в. его называли «марганцовик», а позже «манганес», и использовали при изготовлении финифти пурпурного цвета. Название «марганец» утвердилось в середине XIX в., после перевода на русский язык нескольких популярных руководств и учебников по металлургии (прежде всего книг Валериуса и Перси). Карл Вильгельм Шееле В 1801 г. упоминавшийся выше Дэвид Мюшет – бухгалтер завода в Клайде (Шотландия), занимавшийся пробирным искусством (химическим анализом), обнаружил, что добавки марганца улучшают свойства стали. Д. Мюшет первым начал добавлять в тигельную шихту марганцевую руду с целью получения легированной стали.//
//Реализация технологии тигельной выплавки ферромарганца была впервые осуществлена на практике фабрикантом Пригером в Бонне в 1863 г. Следуя предложениям Бессемера, Пригер производил сплавы в тиглях, которые наполнялись смесью дроблёного чугуна, марганцевой руды, толчёного бутылочного стекла и угольного порошка, и подвергались продолжительному накаливанию в горне с коксом или в печи Сименса, до полного расплавления содержимого. При этом получались сплавы, содержавшие до 60 % (обычно около 25 %) марганца, а также некоторое количество кремния и углерода. Способом Бессемера-Пригера пользовались на многих сталеплавильных заводах, однако вскоре от него отказались из-за высокой стоимости и существенных потерь марганца. Схожий способ предложил Вильямс, в качестве восстановителя использовались углеродсодержащие жидкости – нефть, смола, дёготь и т.п. //
//технология производства ферромарганца в доменных печах была отработана уже к 1880 г. Рассмотрим технологию производства ферромарганца в доменных печах в конце XIX в.
Первым необходимым условием для обеспечения приемлемого уровня содержания марганца в сплаве был подогрев воздушного дутья, подаваемого в печь. По мнению профессора Окермана, одного из основоположников «доменной науки», доменная печь, работающая на древесном угле, используя слабо нагретое дутьё, не может постоянно давать сплав, содержащий даже 50 % марганца. Для получения же сплава, содержащего до 80 % марганца, необходимо использовать в качестве топлива каменноугольный кокс, при этом температура дутья должна составлять 700-800 °С (достигается при помощи воздухонагревателей Каупера или Витвеля).
…
Из-за тяжёлых условий работы для выплавки ферросплавов зачастую использовали доменные печи наиболее простой конструкции – огнеупорная кладка скреплялась железными обручами. Это позволяло с минимальными затратами проводить капитальные ремонты
//
Самая простая высоколегированная сталь, доступная попаданцу — это сталь Гадфилда, содержащая 11-15% марганца, около 1% углерода и 1% кремния. Для этого нужно сплавить 30-40% ферромарганец с необходимым количеством низкоуглеродистого железа.
Гадфилд, изучавший влияние марганца на свойства стали, обнаружил крайне необычные свойства сплава, содержащего около 13% марганца. Сталь была достаточно мягкой, но ее оказалось невозможным обрабатывать любым режущим или абразивным инструментом, поскольку из-за наклепа твердость локально повышалась до твердости инстумента. Кроме того, сталь оказалась немагнитной и плохо проводила электричество.
Сталь Гадфилда, запатентованная в 1886 г., быстро нашла применение для изготовления дробильных валков, зубъев экскаваторных ковшей, крестовин рельсов, а позже гусеничных траков, благодаря сочетанию высокой стойкости к абразивному воздействию и вязкости. Кроме того, из этой стали делали противоосколочные шлемы в Британии во время ПМВ, а также сейфы и прутья тюремных решеток, которые практически невозможно перепилить.
Поскольку такая сталь имеет практически нулевую обрабатываемость, изделия нужной формы желательно получать сразу отливкой, чему способствуют хорошие литейные свойства. С некоторыми предосторожностями марганцевую сталь можно подвергать ковке, а также прокатывать в холодном виде и штамповать.
Ванадий служит универсальным «витамином» практически для любой стали, даже минимальные добавки (0.1-0.2%) повышают предел прочности, износостойкость, измельчают зерно.
Ванадий в небольших количествах практически всегда содержится в магнетитовых рудах (например, в железном песке, из которого делали и делают сталь для японских мечей, 0.3% ванадия), однако при получении стали и железа полностью переходит в шлак, из которого ванадий можно достаточно просто извлечь химическим путем. Еще один потенциальный источник — мухоморы, способные накапливать ванадий в значительных количествах (около 120 мг на кг сырого веса), и асцидии, которые срециально для этого выращиваются в Японии.
Отдельная сложность состоит в восстановлении металлического ванадия — это можно сделать лишь металлотермически, натрием из хлорида или алюминием из оксида. Из-за легкой окисляемости ванадиевую лигатуру нужно добавлять уже в раскисленную сталь.
//В 1905 г., на заре автомобилестроения, во время гонок в Англии одна из французских машин разбилась вдребезги. Один из обломков двигателя этой машины попал в руки Генри Форда, присутствовавшего на состязаниях. Обломок удивил будущего «автомобильного короля»: металл, из которого он был изготовлен, сочетал исключительную твердость с вязкостью и легкостью. Вскоре лаборатория Форда установила, что этот металл — сталь с добавками ванадия.
Не считаясь с затратами, Форд организовал исследования. После нескольких неудач из его лаборатории вышла ванадиевая сталь необходимого качества. Она сразу дала возможность облегчить автомобили, сделать новые машины прочнее, улучшить их ходовые качества. Снизив цены на автомобили благодаря экономии металла, Форд смог привлечь массу покупателей. Это дало ему повод сказать: «Если бы не было ванадия, то не было бы и моего автомобиля».
//
https://znaesh-kak.com/x/n/vanadii/%D0%B2%D0%B0%D0%BD%D0%B0%D0%B4%D0%B8%D0%B5%D0%B2%D0%B0%D1%8F-%D1%81%D1%82%D0%B0%D0%BB%D1%8C
При всех преимуществах тигельной стали производительность такого метода достаточно ограничена, и для выплавки значительных количеств металла сложно применима. Выплавка больших количеств стали возможна методом бессемерования, однако обычный бессемеровский конвертер, знакомый всем со школы, мало подходит попаданцу.
Во-первых, для преодоления гидростатического давления жидкого металла нужен источник дутья с давлением в несколько атмосфер и высокой производительностью.
Во-вторых, в ходе продувки избыточный углерод окисляется лишь до угарного газа, который догорает уже на выходе из конвертера, при этом около 2/3 всего тепла теряется.
Поэтому достаточно сложно поддерживать тепловой баланс процесса, а минимальная загрузка чугуна составляет обычно не менее 10 тонн.
В-третьих, при прохождении воздуха через металл происходит его активное насыщение азотом, что сильно ухудшает свойства получаемой стали, снижает пластичность и вызывает холодноломкость.
Однако практически всех этих проблем можно избежать, используя боковое дутье, впервые предложенное Александром Тропенасом в 1880-х, и применявшееся в так называемых конвертерах малого бессемерования вплоть до середины XX в. для фасонного литья на небольших мастерских. Пример такого конвертера изображен на рисунке.
Конвертер имеет D-образное сечение и футерован кислыми огнеупорами, например, набойкой из кварцевого песка с небольшой примесью глины. Фурмы для вдувания воздуха расположены непосредственно над уровнем заливаемого чугуна, обычно в два ряда. Струи воздуха (достаточно избыточного давления в 0.25-0.5 атмосферы) направляются на поверхность чугуна и выжигают углерод и другие примеси, а образующийся угарный газ догорает непосредственно внутри конвертера за счет добавочного воздуха из верхних фурм, хорошо нагревая металл. За счет этого процесс можно вести даже в очень маленьких конвертерах, с загрузкой лишь в 0.5-0.75 тонны, сталь получается хорошо перегретой, свободной от азота и жидкотекучей.
Ход процесса в малом конвертере практически не отличается от обычного бессемерования. После заливки чугуна с температурой 1200-1300 градусов в горячий конвертер и включения дутья начинает окисляться железо до оксида FeO, который далее переносит кислород примесям — кремнию, марганцу и углероду. В ходе первых минут выгорает только кремний и марганец, при этом вырывающееся пламя небольшое и темное. При сгорании кремния происходит повышениие температуры выше 1500 градусов и начинает активно гореть углерод, пламя сильно увеличивается, и содержимое разогревается еще выше. Когда содержание углерода падает менее 0.2%, плямя опять становиься коротким и появляется дым от сгорающего железа. Если исходный чугун не содержит достаточно кремния (что характерно для древесноугольного чугуна), его нужно сильнее перегревать перед заливкой для того, чтобы углерод стал выгорать сразу же. Вся операция длится 15-20 минут, после чего нужно слить шлак, добавить раскислитель, и, при необходимости, отдельно расплавленный чугун для получения необходимого содержания углерода.
При бессемеровании с кислой футеровкой сера и фосфор практически не удаляются, поэтому нужно использовать свободный от этих примесей чугун. Среди недостатков, характерных именно для конвертеров в боковым дутьем, можно отметить несколько больший угар металла, до 10-15% от исходного чугуна.
Следует отметить, что конвертер даже минимального размера требует не менее 15 тонн чугуна за смену, что значительно выше производительности типичной доиндустриальной домны, дающей в сутки 2-4 тонны металла. Возможно, в этом случае потребуется запускать конвертер только после накопления достаточного количества чугуна, один день в 7-10 дней.
https://chestofbooks.com/crafts/mechanics/Mechanical-Processes/282-The-Tropenas-Converter.html
https://mash-xxl.info/page/085170001144147191155006192061121243005030111228/
Попаданцу может быть также интересен процесс Астона, при котором расплавленная сталь из конвертера выливается в ковш с предварительно расплавленным железистым шлаком с температурой 1200 градусов. При этом происходит доокисление остатков углерода, а застывшее железо образует губчатую крицу, которую остается проковать под механическим молотом для сваривания и удаления шлака. С первого взгляда, может показаться странным превращать жидкую сталь в сварочное железо, но это вовсе не так.
Во-первых, на выходе попаданец получит продукт, привычный местным кузнецам, хорошо поддающийся ковке и кузнечной сварке, и сразу в большом коричестве. Сварочное железо лишено хрупкости, хорошо противостоит коррозии и отлично подходит в качестве конструкционного материала.
Во-вторых, при этом не требуется добавление раскислителей, которые могут быть недоступны попаданцу.
В-третьих, даже небольшие примеси фосфора (выше 0.1%) недопустимы для литой стали; в сварочном железе же даже 0.3-0.4% фосфора обычно мало влияют на свойства металла или даже улучшают их.
При производстве литой стали не обойтись без операции раскисления.
Расплавленное железо способно поглощать значительное количество кислорода (в основном в виде FeO), который при затвердевании расплава реагирует с содержащимся в металле углеродом с выделением угарного газа, образующего пузыри.
Чтобы избежать этого, перед отливкой расплавленную сталь нужно раскислить, то есть добавить небольшое количество веществ с сильным сродством к кислороду.
До открытия раскисления тигельная сталь всегда получалась пористой, и требовала тщательной проковки под молотом, чтобы заварить часть пузырей. Чтобы хоть как-то уменьшить количество пузырей, после расплавления в тигле сталь приходилось дополнительно выдерживать при высокой температуре, при этои происходило частичное раскисление (за счет сдвигания равновесия при повышении температуры, а также увеличения содержания кремния, попадающего из стенок тигля). При этом, однако, сложно было получить воспроизводимые свойства, а сталь сильнее загрязнялась примесями из топлива.
Генри Бессемер, столкнувшийся с пористостью и красноломкостью выплавляемого по его методу металла, сначала решил, что проблема в сере, и попробовал добавлять зеркальный чугун (содержащий 20-30% марганца). Однако проблема была не в сере, а именно в кислороде, и в комбинации с раскислением зеркальным чугуном метод бессемерования смог получить практическое применение.
Основные используемые раскислители — это кремний и марганец. Эти элементы достаточно дешевые, поскольку могут получаться в виде ферросплавов в доменной печи, однако имеют относительно низкую раскисляющую активность, и требуются в количествах порядка процента от массы стали. Алюминий и титан гораздо более активны, и для полного раскисления обычно достаточно сотен граммов на тонну. Многие легирующие элементы, напрмер, ванадий, тоже обладают отличной раскисляющей способностью, хотя их применение таким образом обычно не оправданно.
По степени раскисления сталь делится на кипящую, полуспокойную и спокойную (полностью раскисленную). Надо сказать, что даже в первом случае сталь раскисляют, но используют минимальное количество раскислителей.
Таким образом, попаданцу, желающему внедрить выплавку стали, не обойтись без этого важного приема — раскисления. Получение, например, алюминия, для раскисления тигельной стали будет вполне оправдано даже с использованием натрия. Выплавка же зеркального чугуна не представляет особых сложностей, хотя этот раскислитель и имеет достаточно ограниченную обрасть применения.
Существует еще один способ раскисления, не требующий никаких добавок — вакуумное раскисление, при котором тигель с расплавленным металлом помещается в вакуумную камеру и выдерживается до прекращения кипения. Однако сложно сказать, будет ли сооружение подобной установки проще.
А можно поинтересоваться где марганец копать? Я знаю что он иногда идёт примесью в железный руде (с.м. зеркальный чугун) но это не со всеми рудами бывает.
Про легироание титаном я слышал а вот алюминий в наиболее известных сталях я не видел да и не слишком ли там большая температура чтобы этот алюминий там задержался? Ванадий тоже вещи хорошая особенно если надо твёрдости но где его брать? В Южной Америке или из нефтяной золы?
Кстати интересно а является ли расписание проблемой в мартене?
//где марганец копать?//
Имхо, особых проблем с марганцем быть не должно. Пиролюзит и разные охры, в которых часто много марганца, использовали даже неандертальцы. С Античносьи пиролюзит применяли в стекловарении. В железных рудах марганец встречается очень часто, причем все самые известные с древности центры металлургии обычно как раз работали на рудах с высоким содержанием марганца (штирия, каринтия, даннемора и т.д). Да и просто месторождений марганцеаых руд на самом деле очень много, это весьма распространенный элемент.
//Про легироание титаном я слышал а вот алюминий в наиболее известных сталях я не видел да и не слишком ли там большая температура чтобы этот алюминий там задержался?//
В тех количествах, в которых добавляются раскислители, они обычно не считаются в качестве легирующих добавок, так как практически не влияют на свойства. Хотя тот же алюминий даже в таких маленьких количествах уменьшает зерно, что улучшает сталь, но при этом ухудшает свариваемость.
Алюминий как раскислитель тем и хорош, что очень активен по отношениюк кислороду, заодно удаляет азот, и при этом кипит выше 2000. Кальций, например, кипит при ~1500, а магний при ~1100.
Как полноценный легирующий элемент алюминий тоже вполне применяется — в сталях под азотирование, в магнитных сплавах, современных сталях типа TRIP и TWIP.
//Кстати интересно а является ли расписание проблемой в мартене?//
Мартеновская сталь также требовала раскисления, раскислители сначала добавляли в конце плавки в печь, но уже лет сто любую сталь раскисляют обычно в ковше перед розливом.
А можно подробнее про морскую броню? Вроде как лучшей бронёй WW2, когда этим занимались, это
Class B Armor. Вроде бы это была простая хромо-никелевая сталь с специальной закалкой и внутренним (!) цементированием. Ни молибдена ни ванадия ни вольфрама там нет.
Интересно а из чего сейчас танковую броню кактают? Сейчас основной фокус на всякой керамические которую в эту сталь разными способами пихают. Делать так 12″ бронепояс будет слишком долго.